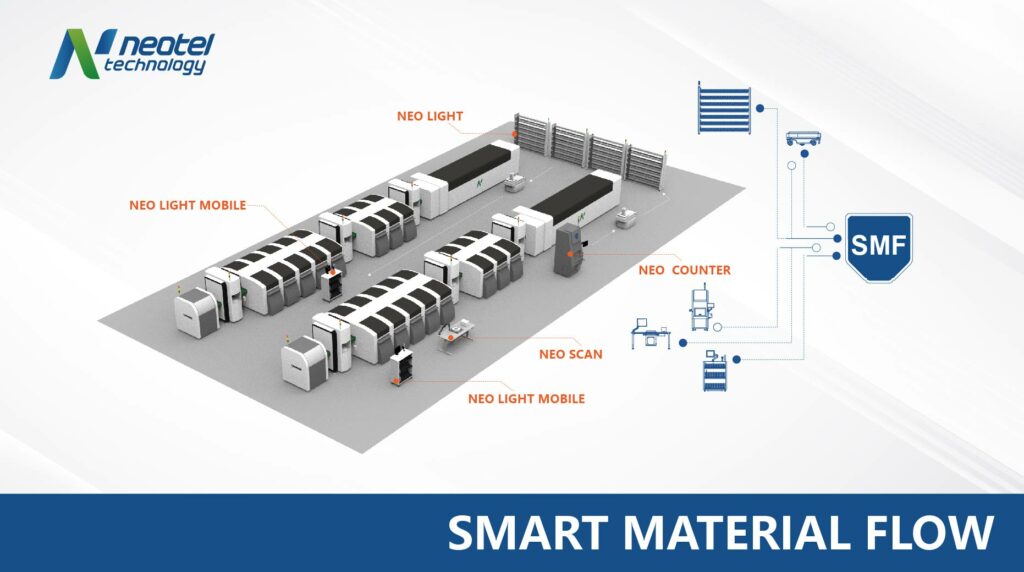
Introduction
Neo Scan Plus from Neotel Technology is a revolutionary product that streamlines reel receiving, barcode recognition, unique generation and print, and label placement processes. This all-in-one solution is designed to maximize efficiency and minimize errors, making it the perfect choice for any operation that needs to improve its organization and accuracy.
Revolutionize Your Reel Receiving
Neo Scan Plus can receive material from AGV or a trolley. The system can be linked to the AGV software and automatically receive the reel stacker from the AGV. Once the reel stacker is in the correct position at the loading port, the system starts to work. This allows for efficient and automated material handling.
AGV
AGV stands for Automated Guided Vehicle. It is a mobile robot used to transport materials and goods on a shop floor or factory setting. AGVs are programmed to follow a specific path. They can be used for tasks such as moving materials to and from manufacturing equipment, transporting finished products to storage or shipping areas, and delivering raw materials to production lines. AGVs can also be equipped with sensors and other technologies to improve their navigation and material handling capabilities. The primary function of an AGV is to automate the transportation of materials, increasing efficiency and reducing labour costs.
Efficient Barcode Recognition with Neo Scan Plus
In the Neo Scan Plus system, cameras are used for image recognition to read the barcode on the existing labels on the material’s surface or reel. The cameras capture an image of the label, and the system uses image processing software to analyze the image and extract the data encoded in the barcode.
Barcode image recognition
The image processing software uses algorithms to locate the barcode in the image and then decodes the data encoded in the barcode. It can work with different barcode types, such as 1D and 2D. Once the data is decoded, the system can then use it to generate a new unique identification code and associates it with the material or reel.
Using cameras for image recognition allows for high-speed and accurate reading of barcodes, even when the labels are partially obscured or damaged. It also eliminates the need for manual scanning and data entry, improving the speed and efficiency of the material handling process.
1D code
1D codes, also known as linear or one-dimensional codes, are barcodes that consist of a series of parallel lines of varying widths and spaces. They can store a relatively small amount of data, typically just a few digits or characters, and are typically scanned using a laser scanner
Commonly used 1D code formats:
Universal Product Code (UPC):
This is the most widely used format for 1D codes and is primarily used to identify products in retail stores. It consists of 12 numerical digits, with the first six digits identifying the manufacturer and the last six identifying the product.
Code 39:
This format is commonly used in manufacturing, logistics, and healthcare. It can store up to 43 characters, including letters, numbers, and special characters.
Code 128:
This format is also commonly used in manufacturing, logistics, and healthcare. It can store a more significant amount of data than Code 39 and can represent all 128 ASCII characters.
Interleaved 2 of 5 (ITF):
This is a widely used format for tracking inventory and shipping in the logistics industry. It consists of bars and spaces where pairs of digits are encoded together.
EAN-13:
This is a variation of the UPC, used primarily in Europe and other countries outside of North America. It consists of 13 numerical digits and is used to identify products in retail stores.
Code 93:
This is similar to Code 39, but it can encode all 128 ASCII characters, mainly used in industrial automation and identification applications.
Codabar:
This simple format is often used in libraries, blood banks, and other applications where a relatively small amount of data needs to be encoded.
2D code
2D codes, also known as matrix or two-dimensional codes, are a type of barcode that consists of a pattern of squares or dots arranged in a grid. They can store much more data than 1D codes and include alphanumeric characters, symbols, and images. 2D codes are typically scanned using a camera or a smartphone.
Some of the most commonly used 2D code formats include:
QR Code (Quick Response Code):
This is the most widely used format for 2D codes. It is used in various applications, including product tracking, marketing, and mobile payments. They can store up to several hundred characters of text or even a small image or video.
Data Matrix:
This format is widely used in manufacturing, logistics, and other industries to store large amounts of data, including serial numbers, production dates, and other identifying information. They can store up to 3,000 characters of data and are typically small enough to fit on even the smallest of products.
PDF417:
This format is commonly used in transportation, logistics, and identification applications. It can store a large amount of data, including text and images, and is often used in ID cards, driver’s licenses, and other forms of identification.
Aztec Code:
This format is similar to a QR code but can store more data in a smaller space. It is commonly used in transportation, logistics, and identification applications.
MaxiCode:
UPS and the US Postal Service primarily use this format for package tracking and delivery. It can store up to 93 characters of data and includes an error correction feature to ensure accurate scanning.
Micro QR Code:
This format is similar to QR Codes but smaller and can store fewer data; it’s mainly used in small spaces such as business cards, jewellery, and other small items.
Han Xin Code:
This is a 2D barcode that is designed to be small and lightweight; it can store a large amount of data, and smartphones can scan it.
Streamline Your Labeling Process with Neo Scan Plus
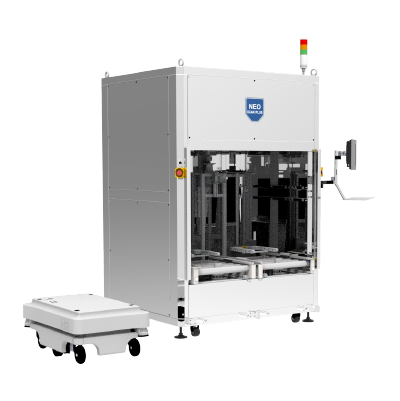
Challenges to Electronics Material Traceability
What is traceability for SMT
In the surface mount technology (SMT) industry, traceability refers to tracking the history of components and materials used to assemble electronic devices. This includes information such as the manufacturer of the components, the date of manufacture, and the batch or lot number. Traceability in the SMT industry is essential for quality control, as it allows for identifying and isolating any defective components or materials that may have been used in the assembly process. Additionally, traceability in the SMT industry is used for compliance with regulations such as RoHS, REACH and JEDEC. It also helps to ensure that the product is safe and reliable.
Work in process material
In the surface mount technology (SMT) industry, “work in process” (WIP) refers to the materials, components, and partially completed assemblies that are in the process of being manufactured or assembled. This includes items that have been received from suppliers and are waiting to be used in the manufacturing process, as well as items that have been partially assembled or tested and are waiting for further processing.
WIP can include raw materials, partially assembled printed circuit boards (PCBs), and completed subassemblies. In SMT production, WIP is tracked to ensure that suitable materials and components are being used at the right time and to monitor the progress of the manufacturing process. It is also used to manage inventory levels and to identify bottlenecks in the production process.
WIP management
The goal of WIP management is to optimize the production process by balancing the flow of materials and components with the capacity of the manufacturing equipment, as well as to avoid too much inventory that can lead to higher production costs.
The traceability of these materials is essential for several reasons. First, it helps to ensure that materials are being used correctly and for the correct purpose. By tracking the movement of materials through the shop floor, manufacturers can identify any issues that may arise, such as defects or contamination. This can help prevent the distribution of faulty or unsafe products, protecting consumers and manufacturers.