パレートの原理
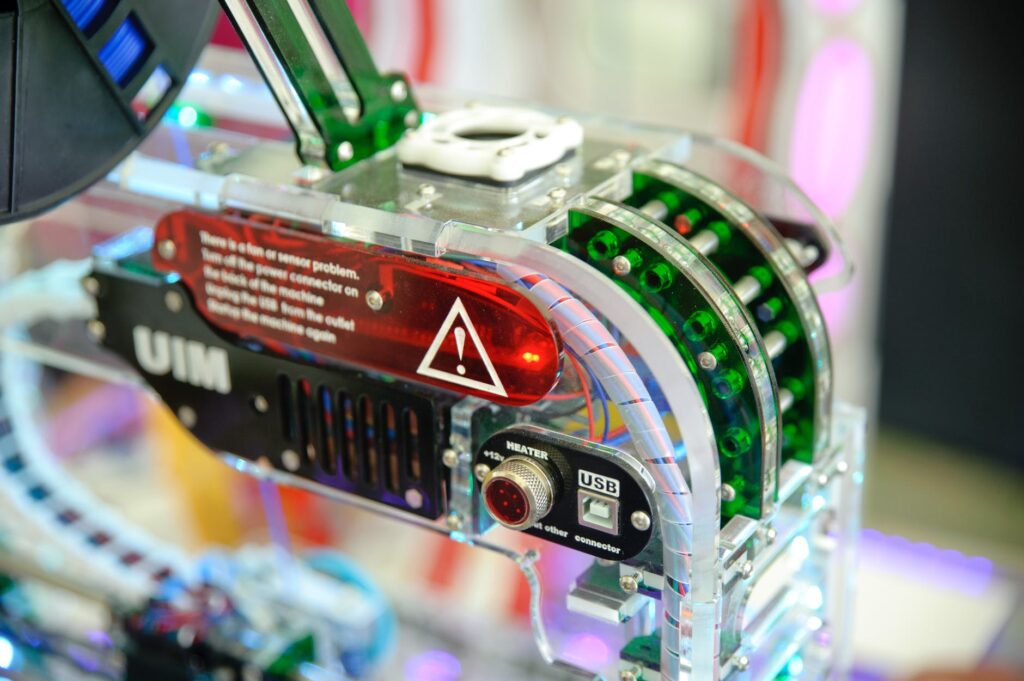
パレートの原理とは? 80/20ルールという言葉を聞いたことがありますか? 20%の原因から80%の結果が生まれるという現象である。 この原理は、生態環境、社会構造、仕事の時間管理、そして言語など、さまざまな分野にわたって作用していることがわかります。 80/20の法則を理解するために、いくつかの簡単な例を紹介します: 80%の仕事は、全労働時間の20%の間に行われる。営業収益の80%は20%の顧客から得られる。問題の80%は、20%の欠陥にたどり着くことができる。この原則は、企業が失敗と成功の重要な要因に優先順位をつけるのに役立ちます。 問題の80%は20%の欠陥によって引き起こされるとすれば、その特定の欠陥を修正することに集中することで、最もポジティブな変化を生み出すことができるのです。 同様に、売上高の80%が20%の顧客から得られているのであれば、その顧客を維持することが有益である。 重要なのは、適切な20%をどのように見つけるか、ということです。 キーポイント パレートの原理とは、「20%の原因から80%の結果が生まれる」という考え方です。 少数派が多数派を支配することが多いという意味です。 ルールといいながら、あくまで自然現象として観察できるものであり、常に80/20の割合になるわけではありません。 企業は、パレート分析やパレート図を使って、最も結果を生み出している効果を見つける。 パレートの法則の他の名称は、「80/20の法則」、「少数精鋭の法則」、「要因疎密の原則」です。 パレートの法則の歴史 パレートの原理は、イタリアの経済学者ヴィルフレド・パレートにちなんで命名されました。 1906年、彼はイタリアの土地の約80%が人口の20%によって所有されていることを観察しました。 この分配を見た彼は、ヨーロッパを旅して同じように富の不平等な分配を観察しました。 彼はこれを「80/20ルール」と呼んだ。 パレートにとって、20%、つまり強力な少数派は、Vital Fewと呼ばれています。 1937年、アメリカの経営理論家ジョセフ・ジュランがパレートの研究を発見し、「80/20ルール」を「パレートの不平等分配の原則」と改名しました。 そして、この原理をビジネスの世界に応用し、「企業がVital Fewに焦点を当てれば、その運営やビジネスの80%にポジティブな影響を与えることができる」という考えに着目したのです。 ずっと80/20分割なのでしょうか? 要するに、ダメなんです。 パレートの原理は、不平等な分布の共通レベルの観察に過ぎない。 最も一般的なのは80/20の配分ですが、決してこれが絶対的な数字というわけではありません。 40%のプロセスが60%の不適合問題に寄与しているというケースもあり得ます。 あるいは、3割の労働者が7割の結果に責任を負っているということです。 では、なぜパレートの原理を使うのでしょうか。 なぜなら、少数派が多数派に対して最大の影響力を持つことが多いという根本的な原則は変わらないからです。 パレートの原理は厳密なルールではないため、パレート分析は、人々や企業がその業務の中で正しい決定要因に集中するためのガイドとして使用されます。 結果は完璧な80/20分割にはならないかもしれませんが、どの要素が最も効果に寄与しているかを示すことができます。 パレート分析の実施方法パレート分析とは、問題点や成功点を洗い出し、優先順位をつけるプロセスです。 パレートのレンズで見ることで、企業は最も大きな影響を及ぼしている問題の解決に集中することができるのです。 不具合が多発している企業は、以下の4つのステップを踏むことで、その最大の要因を特定することができます。 ステップ1:オペレーションに影響を及ぼしている総不具合を特定する。ステップ2:すべての不具合とその頻度を一定期間ごとにまとめたリストを作成する。ステップ3:大きいものから小さいものへ、降順に並べます。ステップ4:総欠陥数に対する各欠陥の累積割合を算出する。このステップを実行するために、あなたがおもちゃの自動車工場を経営し、高級な電子木製の自動車モデルを製造しているとします。 ビジネスは順調だが、問題がある。 この1年間で、合計994件の不具合が発生しましたね。 これは、1営業日あたり平均4件近い不具合が発生していることになります。 何かが必要なのです! ありがたいことに、この1年間の不具合はすべて記録されているんですね。 以上の手順で、特定された不具合、不具合総数、不具合累積数、不具合累積率をまとめた表が出来上がりました。 複雑そうに聞こえるかもしれませんが、かなり簡単で、データを読むのはもっと簡単だと断言します。 ここでは、4つの欠陥(緑色でハイライトされている)があり、全体の欠陥の約80%を占めていることがわかります。 この2割の不良に特化した取り組みをすることで、理論的には全体の8割の不良をなくすことができます。 パレート図の作り方パレート図を作成することで、目の前の課題とその関連性をより深く理解することができます。 パレート図の魔法は、折れ線グラフと棒グラフの両方を兼ね備えていることです。 欠陥の数を正確に把握しながら、その累積値を隣り合わせで理解することができます。 では、この情報をどのようにパレオチャートに反映させればよいのでしょうか。 上の表と同じ情報を使って、下のグラフにまとめると、以下のようになります。 Excelでパレート図を簡単に作成する方法は、最後のビデオでご確認ください。 各バーは1つの欠陥カテゴリーを表し(ここでも上位4つを緑で強調)、左の数字はその頻度を示しています。 […]
個人用保護具(PPE)
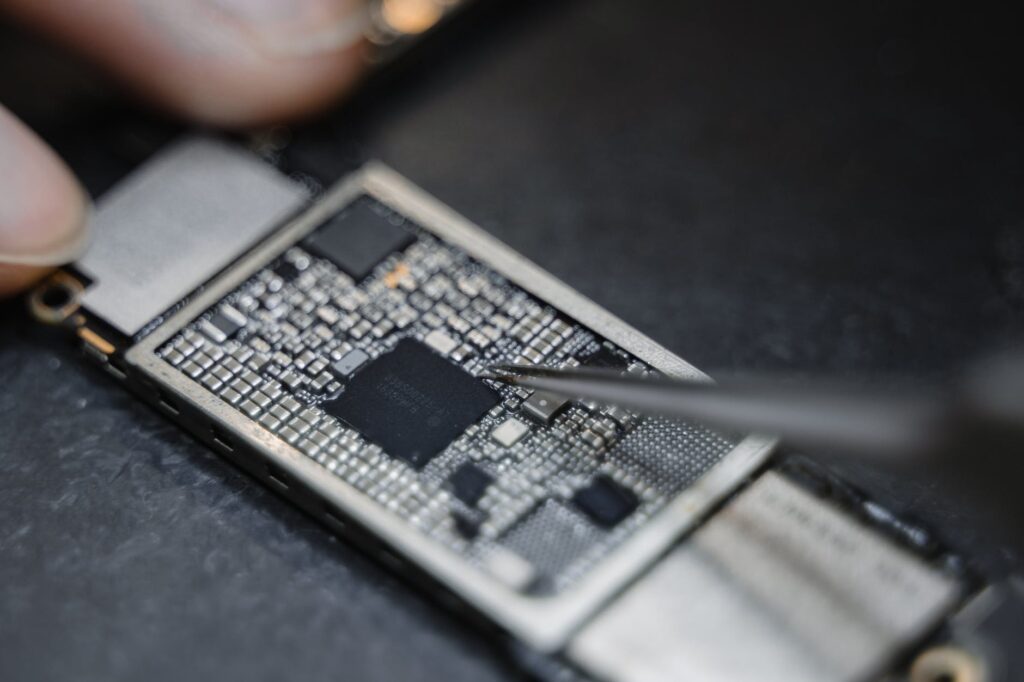
PPEとは? PPE(Personal Protective Equipment)とは、人を傷害から保護するための衣服や身につけられる器具のことを指します。 反射ベスト、ハードハット、安全メガネ、防護服など、挙げればきりがないほどです。 事故や災難は、私たちの日常生活の中で避けられない要素です。 日中は製造現場で働き、夜は養蜂をし、週末はペイントボールで遊ぶなど、PPEは数え切れないほどの人々を重傷や死から救ってきました。 個人用保護具は一見簡単そうに見えますが、PPEの手順を最適化し、従業員の安全を保証するための知的な方法があります。 キーポイント PPE(Personal Protective Equipment)とは、着用者を怪我や害から守るための衣服や着用可能な機器と定義されます。 これには、ハードハット、反射ベスト、聴覚保護具などが含まれます。 PPEに関して言えば、安全は保護と同じくらい機動性が重要です。 作業指示ソフトを使用して、作業者がすべての作業で適切なPPEを使用していることを確認します。 PPEのカテゴリーとその用途 個人用保護具は、保護する部位によって分類されることが多い。 ここでは、最も一般的なPPEの種類と、それらが保護する身体の部位のリストを紹介します。 頭部保護具:ハードハットはその代表例ですが、落下物から頭部を保護するヘッドギアは、危険の多い環境では欠かせません。 顔面保護具安全眼鏡から溶接・研削用マスクまで、顔面保護具は不要な物質や粒子から顔を保護します。 耳の保護見落とされがちですが、耳の健康を維持するためには、耳の保護が重要です。 耳は、伸縮性のあるフォームプラグやノイズキャンセリングヘッドホンで保護することができます。 反射材を使用した服装:目立ちやすい服装は、スピードの速い環境では非常に有効です。 反射パッチは、ベスト、パンツ、ヘッドギアなど、あらゆる衣服に付けることができます。 足と手を守る:足と手は、人体の中でも特に怪我をする頻度が高い部位です。 これらの部位への傷害の多くは致命的なものではありませんが、傷害から安全を守ることは、多くの業界にとって依然として高い優先事項です。 手足の指を保護するために、鋼鉄製のブーツと手袋を使用します。 皮膚を保護するもの:着用者の皮膚を保護する衣服に分類されます。 例えば、溶接工は火花などの高温物から身を守るため、難燃性の溶接ジャケットを着用しています。 病院や危険物取扱所の職員は、皮膚に接触した場合に有害な薬剤から身を守るための完全な防護服を着用します。 呼吸器有害な化学物質を扱うときや、パンデミック(世界的大流行)のとき、肺から有害な物質を取り除くのに役立つのが呼吸器です。 使い捨てのフェイスマスクやフィルター付きのガスマスクなど、簡単なものでよいのです。 安全とは、邪魔をされないこと 製造現場は忙しいものです! 移動する車両、フロアプランの変更、危険物など、作業者を危険にさらす要因はたくさんあります。 ワーカーは安全を確保しつつ、機動性や環境への配慮も必要です。 私たちがunencumberedと言うとき、私たちは文字通りそれを意味します。 作業者が、業界で提供されているすべてのPPEを着用していると想像してください。 彼らは、歩くことができれば、保護するための歩くフン玉になるのです。 これは、彼らの意識を効果的に抑制し、より多くの事故を引き起こす可能性があります。 個人用保護具の意味する安全とは、オペレーターを事故や災害から守ると同時に、動作や視力など本来の能力を発揮できるようにすることです。 もし、安全眼鏡が曇りや傷で視界を妨げているのであれば、そのPPEは本来の目的から外れていることになります。 目は無事でも、滑ったり、つまずいたり、転んだりする経験をしやすくなります。 同様に、聴覚保護によってオペレーターが周囲の状況に気づかない場合、動いている車両に気づかない可能性が高くなります。 この2つの例は、個人用保護具の使用方法について、業界が賢くなる必要があることを示すものです。 製造環境、作業、プロセス、手順はそれぞれ異なる。 すべてのPPE要件を解決する機器や衣服は存在しませんが、スマートな解決策はあります。 PPEには、作業者が適切な作業に適切な機器を使用できるようにするための、インテリジェントなプロセスが必要です。 PPEや安全対策は、実施される作業に合わせてダイナミックに行う必要があります。 個人用保護具を有効に活用する 製造業では、安全眼鏡と鉄指靴が、常に着用しなければならない最低限のPPEの基準となっています。 しかし、ハードハット、聴覚保護具、防毒マスク、難燃性の衣服などが必要な作業についてはどうでしょうか。 企業では、業務の大半を占める作業に応じて、特定のPPEを常時着用することを示す包括的なルールを定めていることが多い。 これは安全性の大部分を確保するのに十分な方法ですが、施設のPPEニーズの100%をカバーするものではありませんし、すべての仕事の特定のニーズに対応するものではありません。 例えば、あるオペレーターが、金属研削盤を使用する珍しい作業を行おうとしています。 […]
ポカヨケ
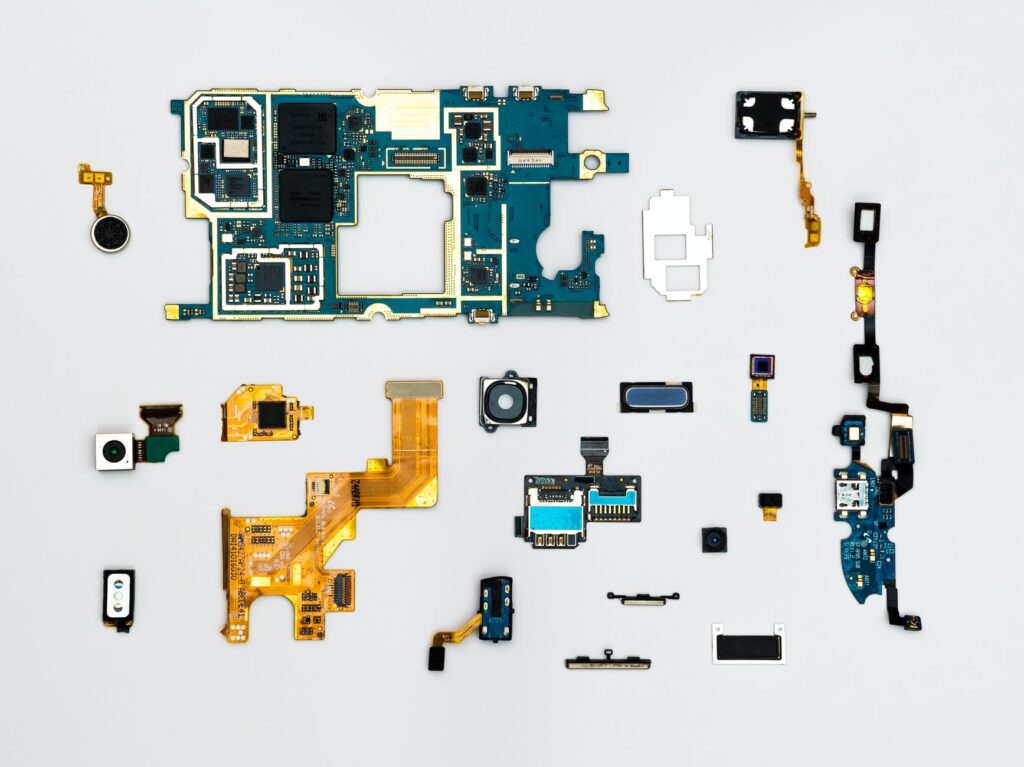
ポカヨケとは、日本語で “間違いを防ぐ””間違えない “という意味です。 ミスが起きにくい、あるいは起きないようにプロセスやシステムを設計することで、ミスやエラーを未然に防ぐことを目的とした品質管理手法のことです。 ポカヨケの概念は、日本の技術者である新郷茂男がトヨタ生産方式の一環として開発したもので、その後、製造工程などの品質向上や効率化のために、世界中の多くの企業で取り入れられています。 ポカヨケの効果・効能 ポカヨケのメリットは以下の通りです: ポカヨケの5種類 プロセスのミスや不具合を防ぐために、ポカヨケにはいくつかの種類があります。 一般的なタイプとしては、以下のようなものがあります: ポカヨケアプリケーション ポカヨケは、製造業、サービス業、オフィス環境など、さまざまな場面や業界で応用することができます。 ポカヨケの応用例として、以下のようなものがあります:
生産性モニタリング
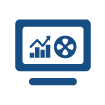
生産性モニタリングとは? 従業員の生産性を把握することは良いことです。 しかし、データを収集し、それを使って生産の最適化を図ることができるのは、素晴らしいの一言に尽きます。 生産性モニタリングは、目標を追跡し、オペレーションの内部構造を理解し、エンゲージメントを通じてワーカーに力を与えることができます。 て行われる: タスクの完了時間を把握する従業員からのフィードバックの場を提供する品質出力のモニタリングリソースの使用状況を観察するどの作業者がどのような作業を行ったかを把握するどの従業員が特定の業務に適格であるかを把握する。従業員が業務に関係のないウェブサイトにどれだけの時間を費やしているかを監視する。そして、もっともっとたくさんのことを!生産性モニタリングは、生産性を向上させ、また低下させる主要な要因を理解する上で、当て推量を排除することができます。 直接観察し、従業員の参加を得ることで、知性と目的を持って情報に基づいた意思決定を行うことができるようになるのです。 キーポイント 生産性モニタリングにより、企業はオペレーターのユニークなレンズを通して、主要な従業員と生産データを収集することができます。 これは、コンピュータの画面を監視したり、従業員のワークステーションからパフォーマンス、品質、生産性のデータを記録したりすることで実現できます。 監視のような考えとよく間違われます。 生産性モニタリングは、労働者に力を与えることも、抑圧することもできます。 やり方やシステムにもよりますが。 生産性モニタリングと製造 製造業には、独自の強みと課題があります。 特に生産性モニタリングに関しては、その傾向が顕著です。 生産性モニタリングは、作業員がFacebookを閲覧していないことを確認するのではなく、2つの重要なアクションを通じて、オペレーションを独自の視点で把握するために使用します: 欠点を見つけて改善する成功を観察し、改善する興味深いのは、生産性モニタリングは、見つけたデータにかかわらず、常にプロセスの改善に役立てることができることです。 なぜなら、知識は力であり、あらゆる要素を追跡し、記録することが可能だからです。 品質がいつもより低下しているのでは? もしかしたら、社員がさらなる指導を必要としているかもしれません。 一部のプロセスで混乱はなかったのでしょうか? 作業指示書のバージョンアップが必要なのかもしれません。 生産性モニタリングとはどのようなものか? あなたが靴工場を経営していて、文字通り雲のような感触の世界で最も快適な靴を作っていると想像してください。 最先端のトップシークレットクッションとフカフカが、ひとつひとつのソールにたくさん入っています。 そのためには、高度なテクニックと実践が必要です。 幸いなことに、あなたは当社の作業指示ソフトウェアを使用して、これらの手順を作業者に案内しています。 さらに、あなたのオペレーションに必要なものを見つけるためのインテリジェントな方法もあります。 生産性レポートを見ると、あるワークステーションがプロセスの完了に時間がかかっていることがわかります。 具体的には、オペレーターが極秘のフラッフ材を取り出すステップで、他のワークステーションに比べて2倍の時間がかかっているそうです。 このステップを問題視して、現場に降りて観察するのです。 そのオペレーターがクッション材を回収するために、より長い距離を歩いていることを実感していますね。 この知識をもとに、必要な資材をより近くに取りに行けるよう、フロアを再編成する方法を考えます。 生産性モニタリングと作業指示ソフトを組み合わせることで、あなたと従業員が問題を発見し、解決策を考え、成功を観察するための多くの方法があります。 生産性モニタリングの注意点 生産性監視は、雇用者と被雇用者の双方にとって、幅広い機能と利点を備えています。 しかし、だからといって、いつも完璧にできているかというと、そうではありません。 従業員はこのような監視を警戒し、最適化よりも監視に重きを置いていると考えることが多いようです。 そして、そこにはある種の真実が存在することもある。 だからこそ、生産性のモニタリングは、VKSのようなスマートなシステムによるインテリジェンスと、正しい姿勢で行う必要があるのです。 生産性モニタリングは、常にオペレーションを最適化し、労働者に力を与えるために使用されるべきものです。 生産性モニターを運用に取り入れる前に、これらの注意点を確認しておきましょう。 責任のなすりつけ合いをなくす 目標を設定する場合、ある仕事を完了するまでの期待時間があります。 しかし、予想された期間内に仕事が終わらない場合、その理由を知りたいと思うでしょう。 これをさらに発展させて、あるタスクに予想以上の時間がかかった場合を例に挙げてみましょう。 オペレーターを責めるのは簡単でしょう。 作業者がプロセスや道具、環境のせいにするのは簡単なことです。 しかし、この「責任のなすりつけ合い」は決して生産的ではありません。 **生産性モニタリングは、推測を排除し、さらに重要なことは、責任転嫁を排除することです。 ** デジタル作業指示書を通じて、マネージャーとスーパーバイザーは生産に役立つ解決策を見つけることに集中します。 これは、経験的なデータを見て、このデータを使ってオペレーションを強化することで実現します。 オペレーターが自分の責任を明確に理解していない場合は、さらにトレーニングの機会を与えてください。 […]
プログラマブルロジックコントローラー(PLC)
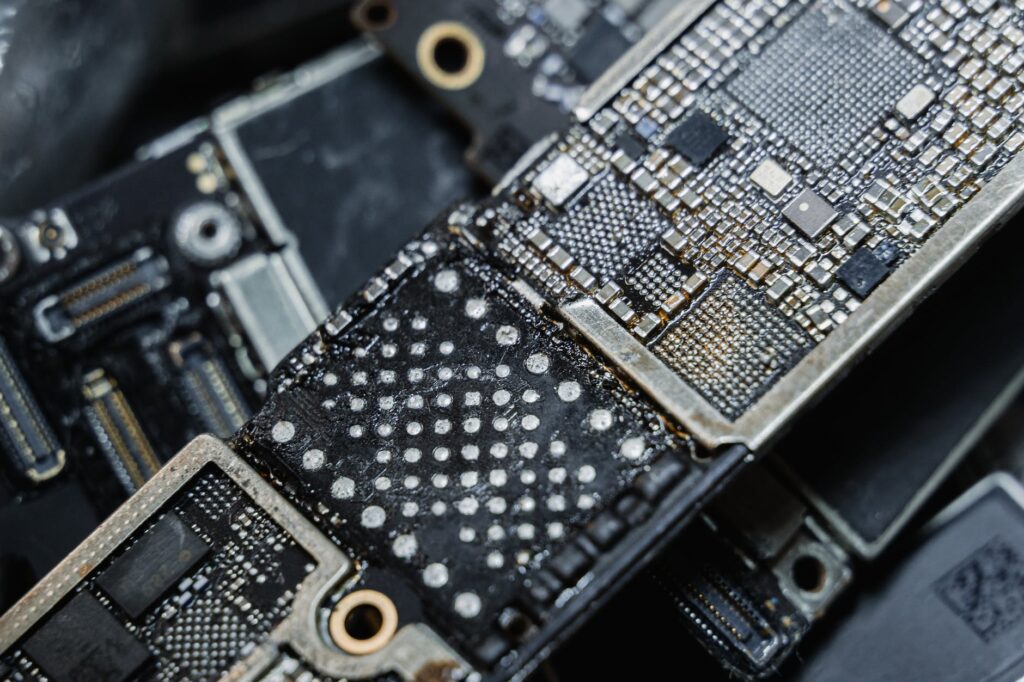
プログラマブルロジックコントローラー(PLC)は、産業用ハードウェアシステムに不可欠なコンポーネントです。 PLCは非エンジニアが使うことを前提に設計されているため、PLCがいかに重要なアプリケーションであり、現場に多くのメリットをもたらすかを理解するには、ほんの少しの努力で十分です。 キーポイント PLC = 入力 + 出力 + CPU ほとんどのPLCがラダーロジック(LD)を採用 PLCはアナログ信号よりディスクリート信号の方が処理しやすい プログラマブルロジックコントローラー(PLC)とは何ですか? プログラマブル・ロジック・コントローラーは、ユーザー・プログラマブル・メモリーを備えたソリッド・ステート・ドライブ(活発に動く部品がないことを意味する)制御システムである。 PLCは、工場で重要な通信や操作の機能を実現するものです: 入出力制御(I/O)論理と算術のルールタイミングとカウント3モードPID制御データ・ファイル処理PLCには、携帯できるほど小さなものもあれば、別の制御室に収めなければならないほど大きなものもあります。 これはもちろん、目の前の産業事業の規模によります。 プログラマブルロジックコントローラーには、2つの選択肢があります:固定式I/Oとモジュール式 固定I/O PLCは、統合型PLCやコンパクトPLCとも呼ばれることがあります。 このタイプは、機械が生み出すあなたの入力と出力が、内部のマイクロコントローラーに完全に統合されている場合です。 つまり、このPLCは内部を一切いじれない不可侵のハードウェアユニットなのです。 モジュラーPLCは、他のモジュールと組み合わせて、入出力プロセッサの組み合わせを作ることができます。 これは、ダウンタイムの減少、故障検出の容易さ、メモリ容量の拡張、カスタマイズされた産業用ソリューションの実現を意味するため、現在では有用なものです。 モジュール式PLCの中には、突発的に1台または複数台の交換が必要になった場合に備えて、バックアップとして保有するものもあります。 PLCの仕組みは? PLCは、データと人間の両方の入力を受けます。 データ入力には、センサー、エンコーダー、ディテクターから自動的に送られる情報が含まれます。 一方、ヒューマンインプットとは、人間が操作システムと対話するためのボタン、スイッチ、キーボード、タッチスクリーン、リモコン、カードリーダーなどを指します。 PLCはこの入力データを受け取り、物理的または視覚的な出力に変換する。 例えば、モーターの始動、バルブの排水、プリントアウトの送信、遠隔地の機器のGPS位置の監視などが挙げられます。 また、出力データは、HMI(Human-Machine Interface)を用いた視覚的な表示の形態とすることも可能です。 しかし、PLCは受け取った入力をどのように読み取っているのだろうか。 プログラマブルロジックコントローラは、信号による入力を読み取り、データを出力に変換する。 信号には、ディスクリートとアナログの2種類があります。 ディスクリート信号のオン/オフ 例:ライトの点灯・消灯のどちらか一方、あるいは機械の刃が所定の位置に下がっているかどうか。 中間的な選択肢はない。 アナログ信号とは、レンジまたは測定値 例)内部温度が80~100度の範囲にあることを記録し、30~45秒の冷却期間を経て次の自動動作を開始した時点で動作ステップを終了するものとする。 初期のプログラマブルロジックコントローラーは、ラダーダイアグラム(LD)言語とも呼ばれるラダーロジックでプログラムされていました。 非エンジニアが読むことを前提に設計されているため、電気回路図がはしご状に描かれ、操作がラングとして描かれていることから、この名がついた。 これは、すべての工程を視覚的に表現することで、作業者がどのような順序で作業を行うかをすぐに理解できるようにするものです。 コマンドの論理的な処理に変更や停止が生じた場合、プログラミングの適切なセクションに迅速かつ効率的にアクセスすることができ、ダウンタイムをできるだけ短くすることができます。 2015年、IECがPLCのプログラミング言語の規格を義務化した。 ほとんどのPLCがラダーロジックを使っていましたが、今ではこんな言語も簡単に使えるようになりました: 構造化テキスト(ST)シーケンシャルファンクションチャート(SFC)ファンクションブロック図(FBD)インストラクションリスト(IL)もちろん、ラダーダイアグラム(LD)はプログラマブルロジックコントローラの定義ロジックです。 これは、PLCが制御する大量かつシンプルなオペレーションは、あまり複雑化しない方がうまくいくからです。 むしろ、あまりに複雑なシステムを使うと、故障が頻発し、どの “はしご “で故障しているのかがわからなくなる。 機器の複雑な工程を後回しにすることで、情報の流れがスムーズになり、初期ロジックに必要なエネルギー消費も少なくなります。 PLCはどんなことに使えるの? プログラマブルロジックコントローラーは、SCADA(監視制御・データ収集)などの制御システムアーキテクチャの重要な部分であり、HMI(ヒューマンマシンインターフェース)技術と容易にコミュニケーションすることで、作業者の理解を深めることができる。 […]
品質マネジメントシステム(QMS)
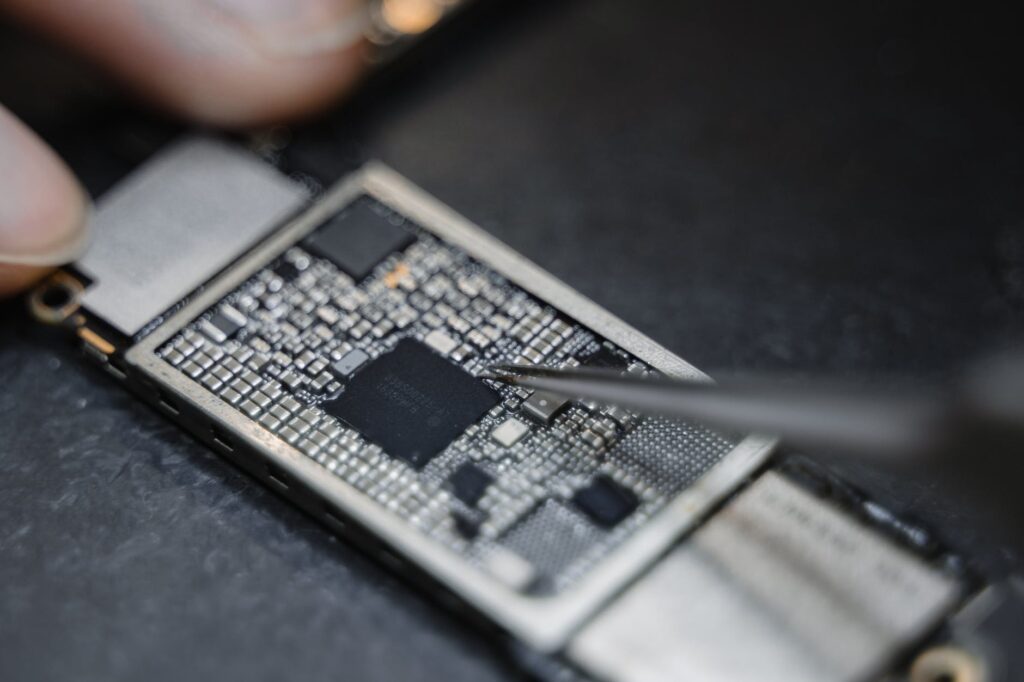
品質マネジメントシステムとは? 品質マネジメントシステム(QMS)とは、特定の業績目標を達成し、品質基準を満たし、業務を継続的に改善することを目的とした一連の業務プロセスおよび手順である。 QMSの多くは、ISO(国際標準化機構)やIATF(国際自動車作業部会)などの規制団体によって作成・運営されていますが、企業が独自に規格や要求事項を作成することもできます。 品質マネジメントシステムは比較的複雑なアプリケーションであるため、導入は企業によって様々です。 しかし、すべてのQMSは、組織内のすべてのプロセスと手順を監督するために設計されていることを忘れてはなりません。 キーポイント 品質マネジメントシステムにより、生産の最適化と品質の向上を図っています。 QMSの代表的なものとして、ISO9001があります。 QMSは、組織の全領域で実施しなければ効果がありません。 企業は作業指示ソフトを活用することで、QMSの遵守を徹底しています。 システムは品質管理にどのように役立つのか? 品質マネジメントを支援するシステムということを理解するために、まず品質マネジメントとは何かということを簡単に説明します。 品質マネジメントとは、企業が行うすべての活動が、特定の性能と卓越性の範囲内で達成されるようにするプロセスである。 一方、品質マネジメントシステムは、望ましいレベルの品質マネジメントを維持するために必要な目標、要件、ベンチマークを確立する手段である。 品質管理は、古典的な4つの要素に分解することができます: 品質計画:現在の業務状況に適合しながら、特定の基準や目標を達成するためのプロセスを設計すること。Quality Assurance(品質保証):生産とサービスの各段階で使用されるプロセスや手順の品質に関するもの。品質管理:製品の欠陥をなくし、品質を向上させることを目的とする。品質向上:プロセスやシステムのパフォーマンスを継続的に調査し、改善するための体系的なアプローチ。 QMSを導入する際に考慮すべき7つの原則 国際的に有名ないくつかの品質マネジメントシステムの主要な貢献者であるISOは、QMSを作成または導入する際に考慮すべき7つの原則を決定しました。 顧客重視:品質を達成するために、QMSは顧客の期待に応え、あるいはそれを超えることに焦点を当てる必要がある。リーダーシップを発揮する:あらゆるレベルのリーダーが団結する必要がある。 企業内のリーダーシップが明確な方向性を持っていれば、QMSの導入は容易になります。人々の参画:QMSが効果的であるためには、すべての従業員が戦略的品質計画に関与し、参加する必要があります。プロセスアプローチ:プロセスを相互接続されたネットワークとして見直す。 この相互接続されたプロセスアプローチにより、ユーザーはオペレーション全体をよりよく理解し、より一貫した結果を得ることができます。改善すること:お客様の期待は常に進化しています。 そのため、QMSには改善のための計画や機会が組み込まれている必要があります。エビデンスに基づく意思決定すべてのQMSは、貴重な洞察とデータを収集するために、VKS作業指示ソフトウェアのような強力なツールを必要としています。関係性管理:最後に、QMSはリレーションシップ・マネジメントを考慮する必要があります。 縦と横の取引関係が適切に管理されることで、健全なサプライチェーンが形成されます。 現代のQMSの内訳 品質マネジメントシステム(QMS)とは、企業が一定レベルのパフォーマンスを維持するためのルール、プロセス、手順、ベストプラクティスの集合体である。 つまり、QMSとは、事業運営を管理し、文書化するための体系的なアプローチなのです。 すべてのQMSは、4つの基本的な構成要素を持っています: 何をするのか言ってみろ(ドキュメント)言ったことを実行する(ドキュメントに従う)言ったことを実行していることを証明する(監査とデータ収集)やることを改善する(継続的改善)そして、これらの各コンポーネントは、あらゆるステークホルダー・グループとその要件に適用されます。 例えば、こんな感じです: お客さまは一定以上の品質を求めます。従業員には十分な労働条件が必要です。政府および規制委員会は、お客様に現行の法律および規制に従うことを要求します。株主は、会社が収益を上げながらコストを下げることを求めています。各グループは、「何をやるか」「それができていることの証明」「継続的な改善のための計画」を明記した何層もの文書が必要です。 このサイクルを繰り返しながら、新たな改良が計画の第一段階となり、時間が経過していきます。 製品品質に関するQMSの実践例 あなたがバブルガム工場を経営していると想像してください。 ブルーベリービューグル」のセリフは、ファンにはたまらないですよね。 しかし、最近、いくつかの矛盾が発生しています。ありがたいことに、まだ製造現場から出たものはありません。 一貫した品質を生み出すために、あなたとあなたのチームは、作業指示ソフトウェアと一緒にQMSを導入します。 上記と同じ4つのコンポーネントを適用するのです。 お客様を満足させるために、各工程の適切な方法をまとめた作業指示書をチームで作成します。労働者は、バブルガムが規制の食品品質対策に準拠するよう、これらの手順に従事し、従います。品質データはすべてのガイドブックに記載され、正しい手順で制作されたことを示し、制作中のエラーをキャッチします。データが観測されると、新しい改善計画が毎月実施されます。QMSを導入しても、要求事項が満たされる限り、ビジネスのどこかを変える必要はありません。 しかし、企業が特定の目標を念頭に置いて、プロセスを観察、管理、最適化する機会を提供するものです。 これは、時間の経過とともに、よりスマートな改良の道を開くものであり、管理団体による認証が必要です。 品質マネジメントシステムの例 QMSの中で最も注目されるのは、ISO9000規格でしょう。この規格は、世界中の製造業やその他の産業において、生産性、効率、顧客満足の象徴となっています。 しかし、企業は特定の品質要件や責任を果たすために、他の多くのシステムを使用しています。 などが挙げられます: IATF 16949:IATF(International Automobile Task Force)が発行する、自動車生産の改善に焦点を当てたQMS。ISO 13485:このQMSは、医療機器製造における特定のガイドラインを遵守するために特に使用されます。ISO22000のこと:食品の安全性を確保することを目的とし、食品製造に関する基準やガイドラインに重点を置いたQMSです。ISO 27001:情報ネットワークの品質と安全性を維持・保護する。AS 9100D:ISO 9001と同じ内容を推進するが、航空、宇宙、防衛の各組織の特定の用途に向けたものである。
冗長性(リダンダンシー
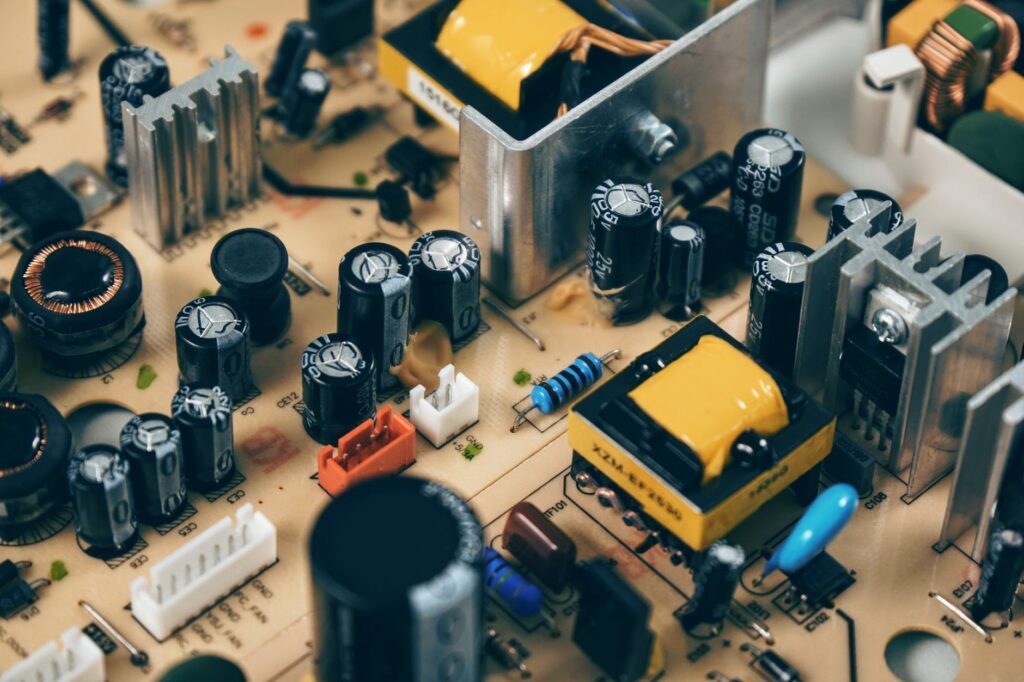
冗長性とは、プロセスにおける反復的で不必要なステップのことで、製造業では、リスク管理およびシステム制御のために生産サイクルに組み込まれた意図的なフェイルセーフ手段のことである。 キーポイント 総合的品質管理(TQM)に使われる技術 目的は、機器やオペレーターの潜在的な故障の範囲を限定することです。 導入コスト<導入しない場合の結果である場合に有用である。 冗長性はどのように役立つのでしょうか? 冗長性は重要です。 冗長性は本当に重要で、重要でさえあります。 ^ 私が何をしたのかわかりますか? トーキングポイントを繰り返すことで、ファクターとしての重要性に特別な注意を喚起しています。 厳密には、第2文は冗長で、内容を繰り返すだけで、新たに役立つ情報を追加していないことを意味します。 もし私が編集するのであれば、2番目の文章は段落の進行を妨げるだけなので、削除します。 しかし、その冗長性に対する批判的な見方は、できるだけ少ない言葉で物事をクリアにすることが目的であるからです。 業界によって、冗長性は意図的で役に立つこともあれば、排除すべきハードルであることもあります。 製造業では、機器の故障や悪条件が重なった場合のフェイルセーフとして、生産工程に意図的に冗長性を持たせることが行われています。 つまり、リスクマネジメントという目的だけのために、何か「余計なもの」が邪魔をするのが良いのです。 冗長性の種類 冗長性の種類は何百とありますが、ここでは一般的に適用されるものを紹介します: ハードウェアの冗長性は、二重または三重のモジュラー冗長性のように、物理的なコンポーネントが二重になっている場合です。情報の冗長性とは、情報の適切なデジタルコピーと保存を保証するチェックの一種で、例えば、電子メールを受信して、それが送信されたとおりのものであると信頼するときのようなものです時間冗長性とは、複数のバッチ処理のように、操作や実行が複数の生産またはサイクルで繰り返されることですソフトウェアの冗長性は、2つのプログラムが同じコードを実行して正確さを比較するように、複数の操作やデータセットを処理するために同等のプログラムを実行するプロセスです複合型(その他)冗長性とは、機械式と油圧式の車両ブレーキのように、上記の種類をいくつか組み合わせてフェイルセーフな冗長性を作ることであり、ソフトウェアとハードウェアの両方の冗長性を利用している。 製造業における冗長性の例 製造業では様々な要素が絡んでくるので、冗長性はかなり大きく変わります。 工場のあるエリアでは、検出されたエラーに関係なく、マシンのパフォーマンスに関するデータを30分ごとに送信するという、極めて明白な時間の冗長性が使用されている場合があります。 VKSのビジュアルワークインストラクションでは、次の生産サイクルを開始する前に、オペレータがディスプレイインターフェースに変数を手動で入力したり、写真を撮影してアップロードするよう求めるプロンプトをカスタマイズすることが可能です。 冗長性は、工場の現場で安全プロトコルや標準的な操作手順について複数のサインを出すような簡単なものでもよいでしょう。 VKSのビジュアルワークインストラクションでは、次の生産サイクルを開始する前に、オペレータがディスプレイインターフェースに変数を手動で入力したり、写真を撮影してアップロードするよう求めるプロンプトをカスタマイズすることが可能です。 冗長性は、工場の現場で安全プロトコルや標準的な操作手順について複数のサインを出すような簡単なものでもよいでしょう。 冗長性を重視する業界 様々な分野の多くの産業が、その分野特有の問題に対処するために、様々なタイプの冗長性に依存しています: メディカルサプライヤーは、医薬品やサービスの需要の急激な変動に対応するため、供給ルートや在庫の冗長性を考慮する。情報技術(IT)は、バックアップファイルやサーバーを使用して、情報が安全でアクセス可能であることを二重にチェックすることで、冗長性の根幹に依存しています。TQM(トータル・クオリティ・マネジメント)のフレームワークを使用したもの例えば、民間航空機は少なくとも2つのエンジンを搭載することが義務付けられているが、技術的には1つのエンジンだけでも運航できるように、航空宇宙は設計上冗長性を持たせている。ヘルスケアでは、研究室や汚染施設において、専門家が流出物や伝染病などの有害物質を「チェック」するために複数のエリアを通過する必要がある場合に、冗長性を使用しています。主要なインフラは冗長性を考慮して構築されている。例えば、センサーや遮断機を使って過電流を検出できる複数のノードを持つ電力線を構築する。産業用製造業では、強力な機械を操作しながら作業者の安全を守るために、冗長性を多用する。 リーン生産は冗長性を利用できるか? リーン生産方式を実践している人たちは、冗長性をリーン生産方式と同時に使用することができるのか、あるいは使用すべきなのか疑問に思っているかもしれません。リーン生産方式が無駄をできる限り排除することを意味するならば、生産ラインに冗長性を意図的に加えることは、そのビジョンを妨害することになるのでしょうか。 無駄な工程を増やすべきではなく、常に排除すべきと言われています。 しかし… 戦略的な冗長性を持たせるために、生産にかかるコスト(金銭的にも時間的にも)を最小限に抑え、もし機器の故障が予測され、時間内に修正されなかった場合、オペレーションに多大なコストがかかることを、さらに深く考えてみてください。 リスクマネジメントのためです。 多くの製造業では、成功や均一性を確保するために冗長性が極めて重要です。 毎日1回、小さく素早く冗長化することで、将来的に突然の故障による破滅的な結果を回避できるのであれば、ほとんどの人は毎日の冗長化に悩まされることはないと思うのですが。 悲惨な結果は、簡単な修正予防策で簡単に軽減されます。 貴社は、冗長性対策を実施するためのコストと、積極的なリスク管理を行わずにプロセスを放置した場合に起こりうる結果のバランスをとるための分析に投資する必要があります。 細かい学術的な証明は必要ですか? でも、読書の宿題は私のせいにしないでね! ジェイコブス大学のこの研究は、製造システム(MS)に冗長性を持たせることで、産業運営の「堅牢性」、すなわち相対的な健全性を高めることをうまく説明しています:“短期的なスケールではMSの冗長性を高めると製造コストが上昇する可能性があるが、むしろ長期的な視点で見ると冗長性はロバストネスを緩衝するのに役立つ。MSの冗長性、ひいては堅牢性を高めることは、MSの不確実性を管理する方法とみなすことができ、これは、例えばリスク分析に直面する製造組織の管理において重要な側面である。” 近藤麻理恵のトレードマークである掃除と整理の方法を用いたリーン生産方式の現代的な分析については、もう少し軽く(いや、かなり軽く)、手早く読みたい方は、こちらをご覧ください。
根本原因分析
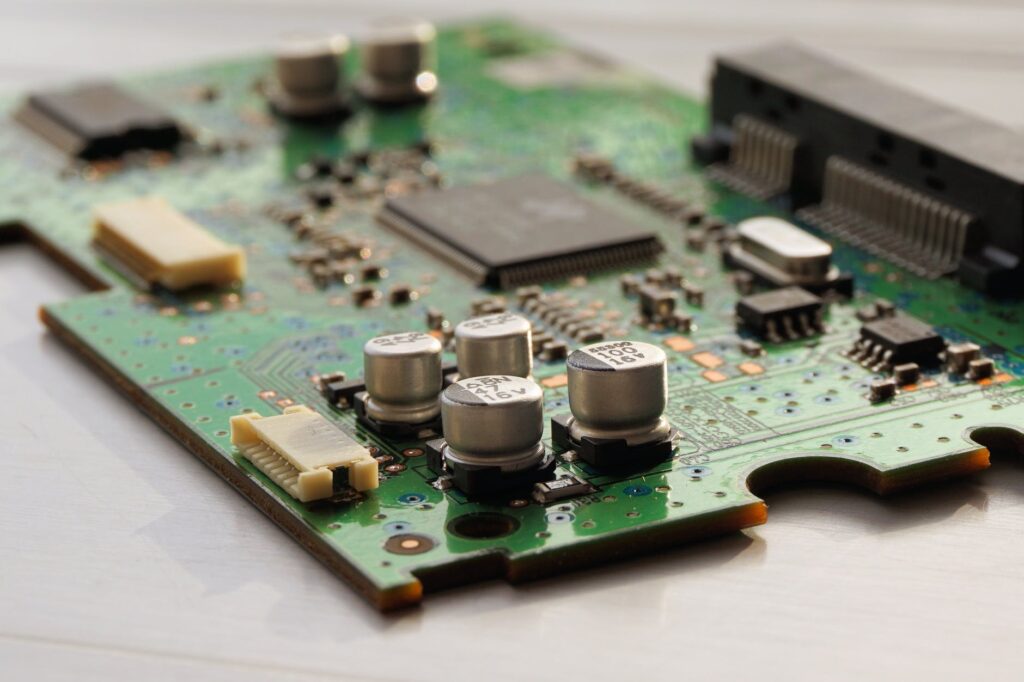
根本原因分析とは? 根本原因分析(RCA)とは、あらゆる不具合、欠陥、問題の根本原因を見つけるために用いられる手法である。 医療、科学、製造/エンジニアリングなどの業界で最も有名ですが、その原理はあらゆる環境で使用できます。 根本原因分析は、問題解決の基本ツールとして、効果的かつ長期的な解決策を講じるために、問題の原因を突き止めることに焦点を当てます。 例えば、足首が痛いと訴える人がいたとします。 単に痛み止めを飲ませることもできますが、それでは痛みの根本的な原因は解決されず、痛みという症状だけが残ることになります。 根本原因分析では、何が起こったのか、なぜ起こったのか、そして再発防止策を発見・定義することができます。 キーポイント 根本原因分析は、さまざまな業界や分野で問題の根本原因を究明するために用いられています。 根本原因分析の4つのステップは、特定、データ収集、因果関係のグラフ化、解決です。 相関因子と寄与因子の区別を必ずつけること。 5Whyやフィッシュボーン図などのツールを使って、因果関係をマッピングする。 原因因子の3分類 製造業をはじめとするあらゆる企業環境において、すべての原因要因は3つのカテゴリーに大別されます。 物理的な原因機械の不具合、工具の破損、インフラの劣化など。人為的な原因ヒューマンエラー、手順の不適切な遵守など。組織的な原因:プロセスが不明確、トレーニング/オンボーディングが不十分、マネジメントが不十分、など。ほとんどの問題や不具合は、複数の原因因子が絡んでいます。 例えば、機械に問題があり(物理的原因)、それがメンテナンス不足によるものであったり、(人的原因)、メンテナンススケジュールが確立されていないことによるものであったり(組織的原因)します。 これをさらに細かく分類することで、問題の根本的な原因をより深く知ることができます。 しかし、この3つの大まかなカテゴリーは、スタート地点として最適です。 根本原因解析の4つのステップ 根本原因分析には様々な方法がありますが、多くの場合、以下の4つの中核的なステップを踏んで行われます。 特定する:このステップでは、何が問題なのか、どんな症状なのか、観察できることは何なのかを確認します。 この識別を確立することで、残りの分析の方向性をより明確にすることができます。データを収集する:利用可能なすべてのデータを収集し、問題のより広い影響を十分に評価する。 結果としての課題から逆算して、その課題につながる触媒をひとつひとつ見つけていくのです。因果関係のグラフ化:今、集めた情報を整理する時です。 5つの理由」または「フィッシュボーン図」のいずれかを使用して、出来事の視覚的な地図または年表を作成する。 これにより、構造化されたビジュアルなフォーマットで、根本原因分析を見つけ、他の人と共有することができます。解決策根本的な原因を突き止めたら、問題を解決するために適切な手段を講じることができます。 可能であれば、根本的な原因を解決することから始め、最初に特定された問題まで解決するようにします。 これができれば、問題点、根本原因、その後の要因を排除することができるはずです。 そうでない場合は、再起動が必要です。 2 根本原因分析の方法 5つの理由 5Whysは非常にシンプルなプロセスなので、ほとんどの根本原因分析で使用できます。 問題を提示されたときに、「なぜ」と5回問うというものです。 そうすることで、表面的な原因因子から究極の根本原因へと段階的に移行することができます。 例えば、御社がチェスタートンのような高品質のメカニカルシールの製造・組立を行っているとします。 余談ですが、VKSを使うことで、トレーニング時間が半分になったって知ってました? シナリオに戻ります。 最近、シールが検査に引っかかることがある。 どうしてですか? オペレーターが正しく組み立てられていない。 どうしてですか? オペレーターは、シールをどのように作るべきかを100%理解しているわけではありません。 どうしてですか? なぜなら、彼らは十分なトレーニングを受けていない新入社員だからです。 どうしてですか? 新入社員に対する十分な研修制度がないからです。 どうしてですか? 会社が労働力の改善や育成を優先していないから。 そしてここに、私たちの仮説の問題の答えが見つかったのです。 このような場合、5Whyはこのようにマッピングされることになります。 さて、Whyの数ですが、堅苦しい決まりはありません。 実際には、3~7個のWhy(なぜ)を問いたいところです。 その範囲内であれば、根本的な原因の掘り下げが不十分である可能性が高いです。 その範囲を超える場合は、天候や世界的な出来事など、自分ではコントロールできない要因に進みすぎている可能性が高いです。 フィッシュボーンダイアグラム […]
ルールエンジン
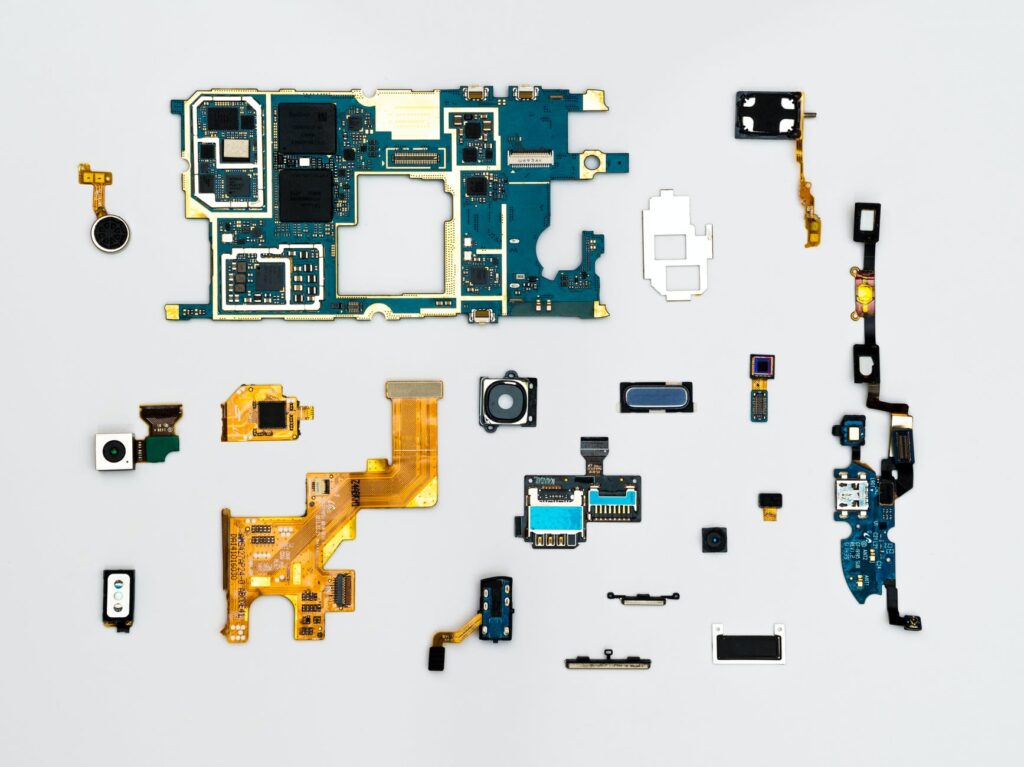
ルールエンジンとは? ルールエンジンは、特定のガイドラインや事前に設定された「ルール」に基づいて製造アクションを自動化することを可能にするロジックの一種である。 これらは、2つの主要な機能で構成されています: 定義された条件;その後の適切なリアクション。現在の状況を見ることで、ルールエンジンは与えられたロジックに基づき、適切なアクションを実行します。 製造システムに確立されたロジックを与えることで、従来は手作業で行っていた工程を自動化することができるようになります。 これにより、適切なアクションが裏側で実行され、オペレーター、スーパーバイザー、マネージャーの貴重な時間が確保されます。 キーポイント ルールエンジンは、特定のガイドラインや事前に設定された “ルール “に基づいて、ビジネスアクションを自動化することができます。 ルールは、少なくとも1つの条件と1つの適切なアクションで構成されます。 ルールエンジンは、多くの場合、IF-THEN式で動作します。 自動化されたルールは、人が付加価値のない仕事をする必要性をなくします。 IF-THENフォーミュラ ほとんどのルールエンジンは、単純なIF-THEN式で動作します: 条件Xが発生したら、アクションYを実施する。 この公式がうまく機能する理由は、曖昧な言葉を取り除き、特定のパラメータに基づいた明確な枠組みを提供するためです。 パスタの茹で方を説明するとき、パスタをお湯に入れるタイミングと、取り出すタイミングを説明することを想像してください。 IF-THEN式で、前の条件が満たされないと次のルールを考えることができないような、順を追った指示を出すことができます。 お湯が沸騰している場合(約100℃)は、沸騰したお湯の中にパスタを入れる。パスタが茹で汁の中に5分ほど入っていたら、取り出して水気を切る。 マニュファクチャリングルールエンジン 製造環境の中では、ルールを組み合わせて特定のプロセスを自動化し、インテリジェントで応答性の高いシステムを構築することができます。 ここでは、在庫管理のために特別に作られたルールエンジンを紹介します。 銅線#GH784の在庫が1500本以下になったら、1000本追加注文する。銅線#GH784の在庫が750本以下になったら、リードタイムが2日必要な重要なアセンブリを優先する。 銅線#GH784の在庫が3000個を超えたら、オペレーションマネージャーに連絡してください。 銅線#GH784が注文できない場合は、在庫管理チームに連絡してください。 このシンプルなルールを分解してみましょう。 上記のルールエンジンは、自律的に部品を発注し、生産ニーズに対応し、必要なときに適切な担当者に通知します。 どんな状況でも、ルールエンジンはメーカーが成功するために必要な在庫と知識を確保する。 これにより、オペレーターや他のメンバーは他の業務に集中することができ、ルールエンジンは在庫を円滑に管理することができます。 非付加価値作業を自動化する3つの方法 仕方がないことなんです:製造業には、付加価値のある仕事と付加価値のない仕事があります。 しかし、ルールエンジンを使うことで、社員が行うべき非付加価値の作業を減らすことができるのです。 ルールエンジンによるプロセスの自動化について、3つの例をご紹介します。 適切な人に自動で通知するオペレーターが業務を遂行する際には、アセンブリの品質に目を光らせる必要があります。 また、オペレーターが品質不良を発見した場合、オペレーターが旗を立て、上司を探し、詳細に報告する必要があり、その結果、作業に時間がかかり、業務が滞ってしまいます。 しかし、ルールエンジンと作業指示ソフトウェアが確立されていれば、オペレータが製品に品質上の問題があることを指示すると、ルールエンジンが率先してデータを収集し、必要な人に伝達することができます。 このルールエンジンは、このような形になります: ユーザーが品質上の問題を確認した場合は、「本体を赤いビンに入れる」ように通知します。ユーザーが記入するための不適合フォームを開く。情報がファイルされている場合は、すべての情報を品質管理部に送信します。問題が報告されたら、ユーザーをステップ1に連れて行き、新しいアセンブリを開始できるようにします。ここでは、ルールエンジンが、情報やデータを適切な人に届けると同時に、オペレーターに次の行動を指示する役割を担っていることがわかります。 これにより、15分の工程が2分の工程になります。 安全リマインダーの自動化仕事によっては、さまざまなレベルの安全装置が必要です。 従業員に適切な安全手順と装備を思い出させることは、現場で従業員の安全を守るために最も重要です。 インテリジェントなルールエンジンを導入することで、メーカーは従業員に特定のリスク、必要なPPE、目の前の仕事の状況に関するベストプラクティスの最新情報を通知することができます。 このルールエンジンでは、次の2つのルールが表示されます: 作業指示番号がH(危険)で始まる場合は、各ガイドブックの冒頭に危険なPPEに関する注意事項をユーザーに表示する。作業指示番号がW(溶接)またはG(研削)で始まる場合、各ガイドブックの冒頭にユーザーへの換気注意事項を表示します。ルールエンジンは、オペレーターが業務を適切に遂行するために必要な正しい安全衛生情報を受け取ることができるように、舞台裏で機能しています。 メンテナンス作業指示書を作成する機械は定期的なメンテナンスが必要です。 どの機械に修理が必要かを把握するため、メンテナンス担当者は機械の稼働時間を手作業で点検し、予防的な業務を監視してスケジュールを立てることが多い。 長いけど必要なプロセスだ…少なくとも以前はそうだった。 インテリジェントなルールエンジンと作業指示ソフトウェアにより、この長いプロセスを完全に取り除くことができます。 あなたの会社には、1000時間の稼働ごとに修理が必要なプレス機械があるとします。 オペレーターは毎日これらの機械を使用しており、使用前の事前点検が義務付けられているため、デジタル指示書に時間を記録することは理にかなっています。 1台のマシンが1日8時間、週5日使用される場合、1ヶ月に約180時間使用されることになり、約6ヶ月に1度メンテナンスが必要になると判断されました。 これはオペレーションの高低によって変動するため、数値には注意が必要です。 メンテナンス部門に時間を知らせるスマートなシステムが必要だが、あまり多くの通知を送りたくはない。 あなたのチームは、次のようなシステムのルールセットを作成します: […]
シックスシグマ
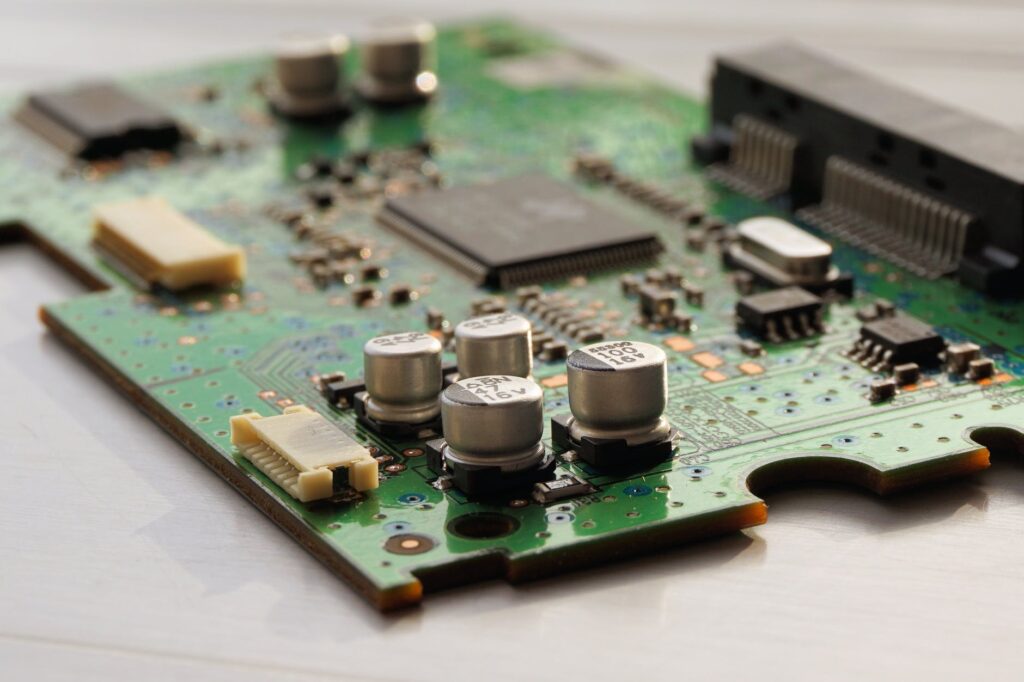
シックスシグマとは、多種多様な統計解析「ツール」と「テクニック」を用いて、生産工程における品質不良の削減を目的とした経営理念です。 リーン生産方式、アジャイル生産方式、総合生産保全方式(TPM)、そして比較的似ている(しかし機能的には異なる!)リーンシックスシグマなど、他の生産方式から要素を借用した堅牢な方法論です(いくつか例を挙げます)。