PDCAサイクル
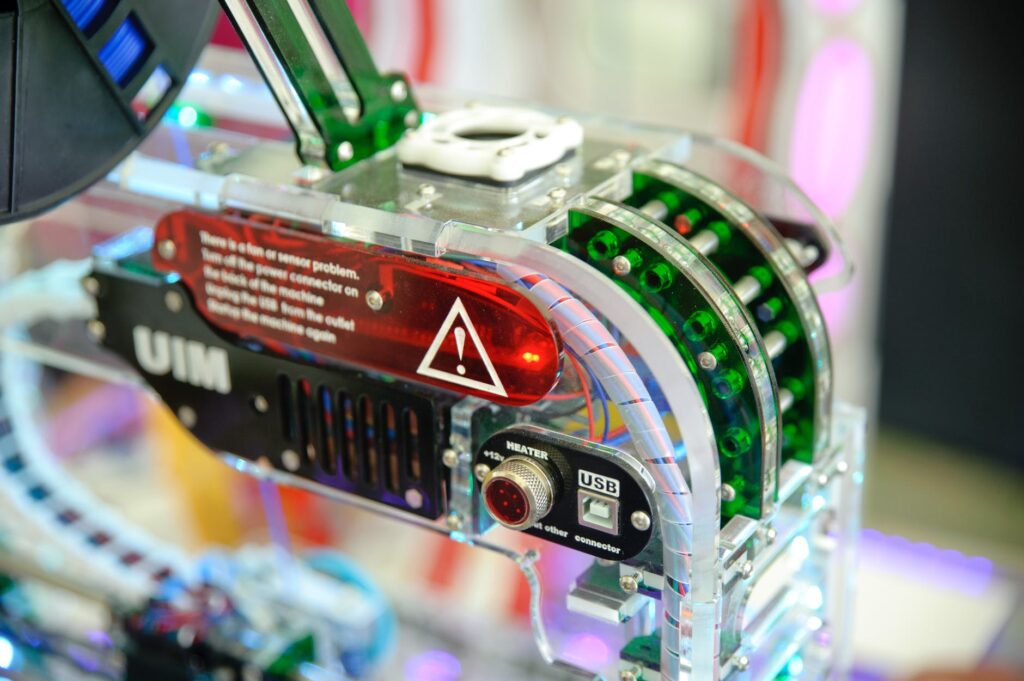
PDCAサイクルは、継続的な改善のステップをプロジェクトごとに計画し、区別するためのシンプルかつ効果的なツールです。 PDCAサイクルは、シックスシグマやトータルクオリティマネジメントの経営理念でよく使われる反復的なツールです。 キーポイント Plan-Do-Study-Act、Deming、Shewhartサイクルとも呼ばれる。 4つのステップPlan、Do、Check、&Act PDCAを回すことでカイゼンを促す。 チームが継続的な改善を重視すると言うのは簡単ですが、長期にわたって実行するのは難しいものです。 PDCAサイクルは、カイゼンを4つの管理可能な領域に分解することで、従業員を循環的な改善パターンに導くのに役立つ。 PDCAサイクルのバリエーションが生まれた歴史的背景 PDCAサイクルの最初の事例を特定するのは、やや困難です。 このサイクルは、20世紀半ばに活躍した統計学者であり、革新的な経営指導者であったウィリアム・エドワーズ・デミングに由来するとする説が有力です。 デミングは、師匠であるウォルター・A・シューハートからインスピレーションを受け、当初このプロセスを “シューハート・サイクル “と名付けました。 やがて、PDSA(Plan-Do-Study-Act)サイクルと呼ばれるようになり、時には「デミングホイール」とも呼ばれるようになりました。 しかし、この循環型プロセスの起源はさらに遡り、フランシス・ベーコン卿が開発した科学的手法にあります。科学的手法は、体系的な実験と論理的な結論によって仮説を検証することに重きを置いています。 PDCAは何のためにあるのか? PDCAサイクル、または関連する頭字語はどれでも構いませんが、一般的に4つの発展段階があります: ステップ1:計画 科学実験のプロセスや仮説、必要な材料、導入研究の概要を説明せずに実験を始めることはないでしょう? そのため、重要な生産工程を修正・改善しようとする場合、余計な変数に手を加える前に、完全な攻撃計画を概説することが賢明である。 計画段階は、PDCAサイクルの他の重要な段階で選択するための選択肢のマップを持つために、可能な限り詳細な情報を提供する必要があります。 優れた科学者は偶然を見逃さず、優れた経営者はあらゆる可能性を考慮し、迅速に適応して無駄を省く。 ステップ2:Do PDCAサイクルを回す際にリーダーが陥りがちなのが、「Doing」の部分を強調しすぎることです。 たとえそれが非常に魅力的で能動的なステップであっても、変化を実行すること(すなわち「実行すること」)は、計画段階の二の次であるべきです。 このステップを予想以上に小さくする理由は、このステージで使用するすべての行動計画は、事前にプランニングで確立されていなければならないからです。 Doingは、計画プロセスの延長に過ぎない。 PDCAサイクルは、教科書のエッセイのようなものだと考えてください。最初の段落では、メイントピックや仮説など、取り上げたい概念を紹介します。 そして、第2パラグラフでは、イントロダクションで取り上げたコンセプトをさらに発展させています。 農業技術に関するエッセイを読んでいて、著者が突然スーパーマーケットのサプライチェーンの話に切り替えたとしたら、その微妙なつながりはわかるかもしれませんが、著者の主張の本筋がわからなくなってしまうでしょう。 PDCAサイクルは、トピックからトピックへとあちこち飛び回ることでわかりにくくならないように、計画段階の続きを論理的に追い、サイクル全体のマップを頻繁に参照するようにしましょう。 ステップ3:チェック PDCAサイクルの第3ステージは、第2ステージで発生した「やる」ことの結果を「確認」することです。 デミングは、この第3ステップを「チェック」ではなく「スタディ」と呼んだと言われていますが、プロセス改善の種類によっては、どちらも適切です。 このステップの目的は、プロセス実験から得られたデータを検証することです。 これは、いくつかの異なる方法で行うことができます: 新しいプロセスを監査するために第三者に依頼し、ギャップがないかをチェックする。実験プロセスを同様の条件で繰り返し、確実に効果を出すこと異なる条件下で実験プロセスを繰り返し、プロセスの効果の限界を検証する。プロセスの拡張性を検証するために、範囲と参加者を拡大する。自社データと、成果が実証されている査読付き研究との比較データを「チェック」する方法はさらにたくさんあるので、プランニングセクションの中で、どのデータセットをどのように定量化するのか、幅広い質問をするようにしてください。 ステップ4:行動する 第4ステップの「行動」は、テストされ承認された変更を実行することと、その変更の長期的なモニタリングを確立することの2つの重要性を持っています。 プロセスが改善され始めたら、その改善水準を維持するための基準を導入し、次のプロセス改善へとつなげたいものです。 先回りして結論を出すようなマネジャーにはならないようにしましょう! あなたのチームがPDCAサイクルの段階を丹念に回しているのは、最初から正しく行い、時間をかけてプロセスを自給自足させたいからです。 PDCAサイクルの活用によるメリット PDCAは、組立ラインのカイゼンや部門間の責任分担の見直し、さらにはまだ導入されていない新基準の実験に使うなど、ほぼ普遍的な応用が可能です。 ここでは、観察可能な効果の一部をご紹介します: リーダーシップの停滞期からの脱却をサポート改善を追求する風土を醸成する進行中のプロジェクトの今後のタスクを明確化する大きな変化を起こす前に、小規模なテストを行う標準化を実現します。イノベーションを促進する創造的な問題解決と実用的な解決策を奨励する。 PDCAループを閉じる:次に来るのは? PDCAループは1つのプロジェクトを指すものであり、プロジェクトごとにサイクルを分けることで、タスクの分割や進捗の確認が容易になります。 しかし、終わりのないToDoリストからようやく何かをチェックできたときの喜びはひとしおで、新しく改善された生産工程を、PDCAの手法によって「修正された」と思って放棄する誘惑もある。 継続的な改善には終わりがない! だからこそ、新しいプロセスを監視するために、他の人が最終的にターゲットになるようなチェックとバランスを実装することが非常に重要です。 システムという以上に、サイクルなんです! 大きなプロセスを、計画、テスト、チェックといった小さな段階に分けることで、有益な変化を維持することが管理しやすくなり、追跡も容易になります。
PDCA-Zyklus
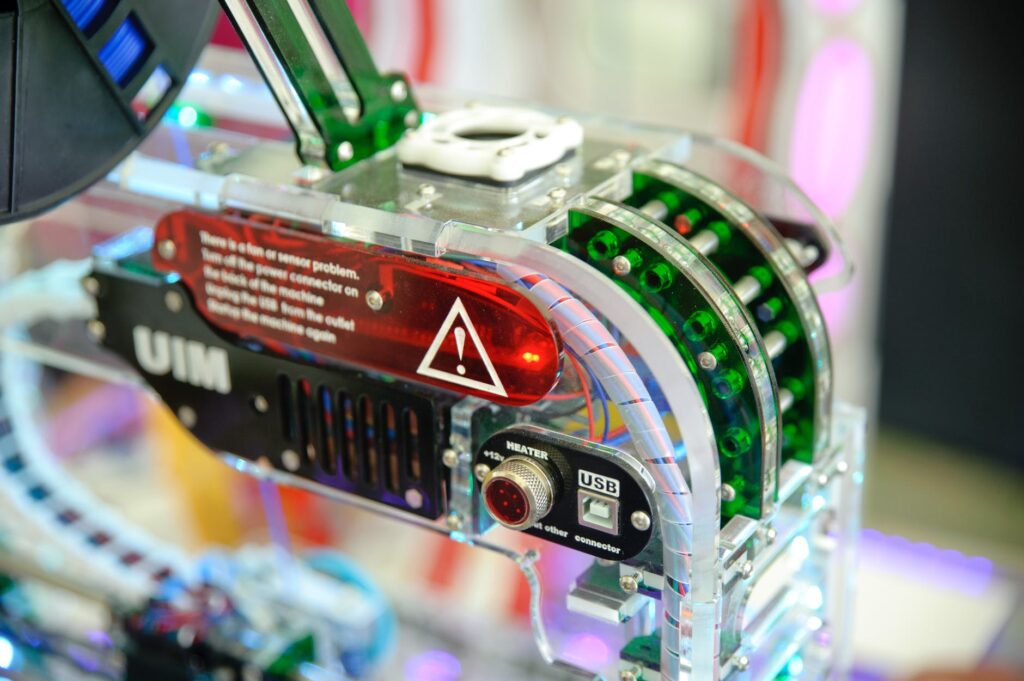
Der PDCA-Zyklus ist ein einfaches, aber wirksames Instrument, um die Schritte der kontinuierlichen Verbesserung projektspezifisch zu planen und zu differenzieren. Er ist ein fester Bestandteil jeder Variante der institutionellen Qualitätskontrolle. Der PDCA-Zyklus ist ein iteratives Instrument, das häufig in den Geschäftsphilosophien Six Sigma und Total Quality Management verwendet wird. SCHLUSSFOLGERUNGEN Auch bekannt als Plan-Do-Study-Act-, Deming- […]
PDCA Cycle
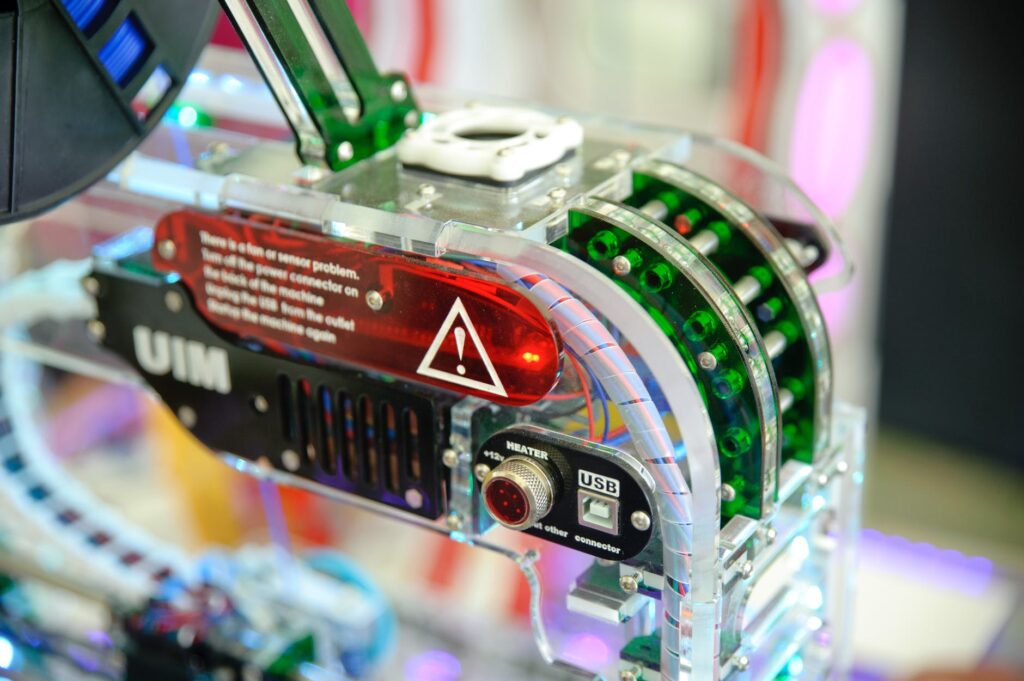
A staple of any variation of institutional quality control methodology, the PDCA Cycle is a simple yet effective tool to plan and differentiate the steps of continuous improvement on a per-project basis. The PDCA Cycle is an iterative tool that is commonly used in the Six Sigma and Total Quality Management business philosophies. KEY TAKEAWAYS […]
PDCA Cycle
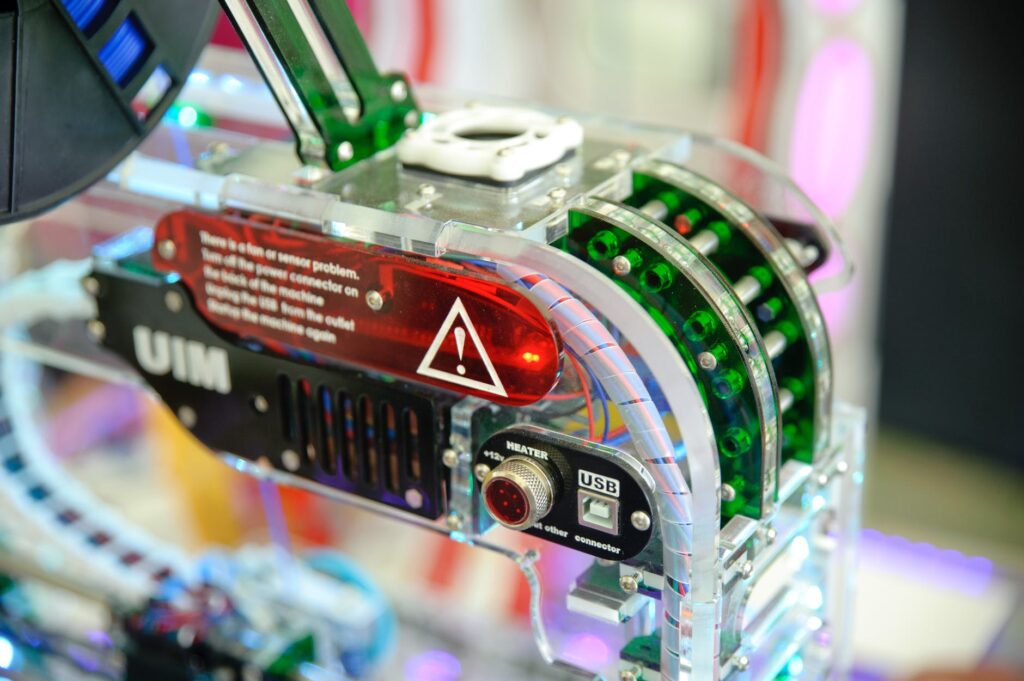
A staple of any variation of institutional quality control methodology, the PDCA Cycle is a simple yet effective tool to plan and differentiate the steps of continuous improvement on a per-project basis. The PDCA Cycle is an iterative tool that is commonly used in the Six Sigma and Total Quality Management business philosophies. KEY TAKEAWAYS […]
パレートの原理
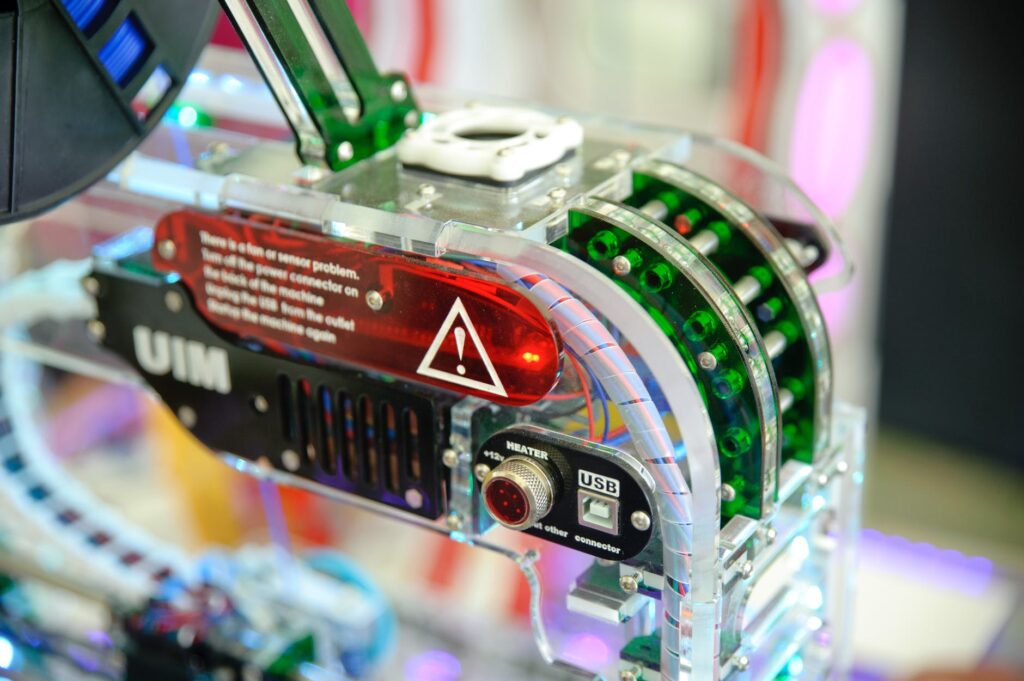
パレートの原理とは? 80/20ルールという言葉を聞いたことがありますか? 20%の原因から80%の結果が生まれるという現象である。 この原理は、生態環境、社会構造、仕事の時間管理、そして言語など、さまざまな分野にわたって作用していることがわかります。 80/20の法則を理解するために、いくつかの簡単な例を紹介します: 80%の仕事は、全労働時間の20%の間に行われる。営業収益の80%は20%の顧客から得られる。問題の80%は、20%の欠陥にたどり着くことができる。この原則は、企業が失敗と成功の重要な要因に優先順位をつけるのに役立ちます。 問題の80%は20%の欠陥によって引き起こされるとすれば、その特定の欠陥を修正することに集中することで、最もポジティブな変化を生み出すことができるのです。 同様に、売上高の80%が20%の顧客から得られているのであれば、その顧客を維持することが有益である。 重要なのは、適切な20%をどのように見つけるか、ということです。 キーポイント パレートの原理とは、「20%の原因から80%の結果が生まれる」という考え方です。 少数派が多数派を支配することが多いという意味です。 ルールといいながら、あくまで自然現象として観察できるものであり、常に80/20の割合になるわけではありません。 企業は、パレート分析やパレート図を使って、最も結果を生み出している効果を見つける。 パレートの法則の他の名称は、「80/20の法則」、「少数精鋭の法則」、「要因疎密の原則」です。 パレートの法則の歴史 パレートの原理は、イタリアの経済学者ヴィルフレド・パレートにちなんで命名されました。 1906年、彼はイタリアの土地の約80%が人口の20%によって所有されていることを観察しました。 この分配を見た彼は、ヨーロッパを旅して同じように富の不平等な分配を観察しました。 彼はこれを「80/20ルール」と呼んだ。 パレートにとって、20%、つまり強力な少数派は、Vital Fewと呼ばれています。 1937年、アメリカの経営理論家ジョセフ・ジュランがパレートの研究を発見し、「80/20ルール」を「パレートの不平等分配の原則」と改名しました。 そして、この原理をビジネスの世界に応用し、「企業がVital Fewに焦点を当てれば、その運営やビジネスの80%にポジティブな影響を与えることができる」という考えに着目したのです。 ずっと80/20分割なのでしょうか? 要するに、ダメなんです。 パレートの原理は、不平等な分布の共通レベルの観察に過ぎない。 最も一般的なのは80/20の配分ですが、決してこれが絶対的な数字というわけではありません。 40%のプロセスが60%の不適合問題に寄与しているというケースもあり得ます。 あるいは、3割の労働者が7割の結果に責任を負っているということです。 では、なぜパレートの原理を使うのでしょうか。 なぜなら、少数派が多数派に対して最大の影響力を持つことが多いという根本的な原則は変わらないからです。 パレートの原理は厳密なルールではないため、パレート分析は、人々や企業がその業務の中で正しい決定要因に集中するためのガイドとして使用されます。 結果は完璧な80/20分割にはならないかもしれませんが、どの要素が最も効果に寄与しているかを示すことができます。 パレート分析の実施方法パレート分析とは、問題点や成功点を洗い出し、優先順位をつけるプロセスです。 パレートのレンズで見ることで、企業は最も大きな影響を及ぼしている問題の解決に集中することができるのです。 不具合が多発している企業は、以下の4つのステップを踏むことで、その最大の要因を特定することができます。 ステップ1:オペレーションに影響を及ぼしている総不具合を特定する。ステップ2:すべての不具合とその頻度を一定期間ごとにまとめたリストを作成する。ステップ3:大きいものから小さいものへ、降順に並べます。ステップ4:総欠陥数に対する各欠陥の累積割合を算出する。このステップを実行するために、あなたがおもちゃの自動車工場を経営し、高級な電子木製の自動車モデルを製造しているとします。 ビジネスは順調だが、問題がある。 この1年間で、合計994件の不具合が発生しましたね。 これは、1営業日あたり平均4件近い不具合が発生していることになります。 何かが必要なのです! ありがたいことに、この1年間の不具合はすべて記録されているんですね。 以上の手順で、特定された不具合、不具合総数、不具合累積数、不具合累積率をまとめた表が出来上がりました。 複雑そうに聞こえるかもしれませんが、かなり簡単で、データを読むのはもっと簡単だと断言します。 ここでは、4つの欠陥(緑色でハイライトされている)があり、全体の欠陥の約80%を占めていることがわかります。 この2割の不良に特化した取り組みをすることで、理論的には全体の8割の不良をなくすことができます。 パレート図の作り方パレート図を作成することで、目の前の課題とその関連性をより深く理解することができます。 パレート図の魔法は、折れ線グラフと棒グラフの両方を兼ね備えていることです。 欠陥の数を正確に把握しながら、その累積値を隣り合わせで理解することができます。 では、この情報をどのようにパレオチャートに反映させればよいのでしょうか。 上の表と同じ情報を使って、下のグラフにまとめると、以下のようになります。 Excelでパレート図を簡単に作成する方法は、最後のビデオでご確認ください。 各バーは1つの欠陥カテゴリーを表し(ここでも上位4つを緑で強調)、左の数字はその頻度を示しています。 […]
Pareto-Prinzip
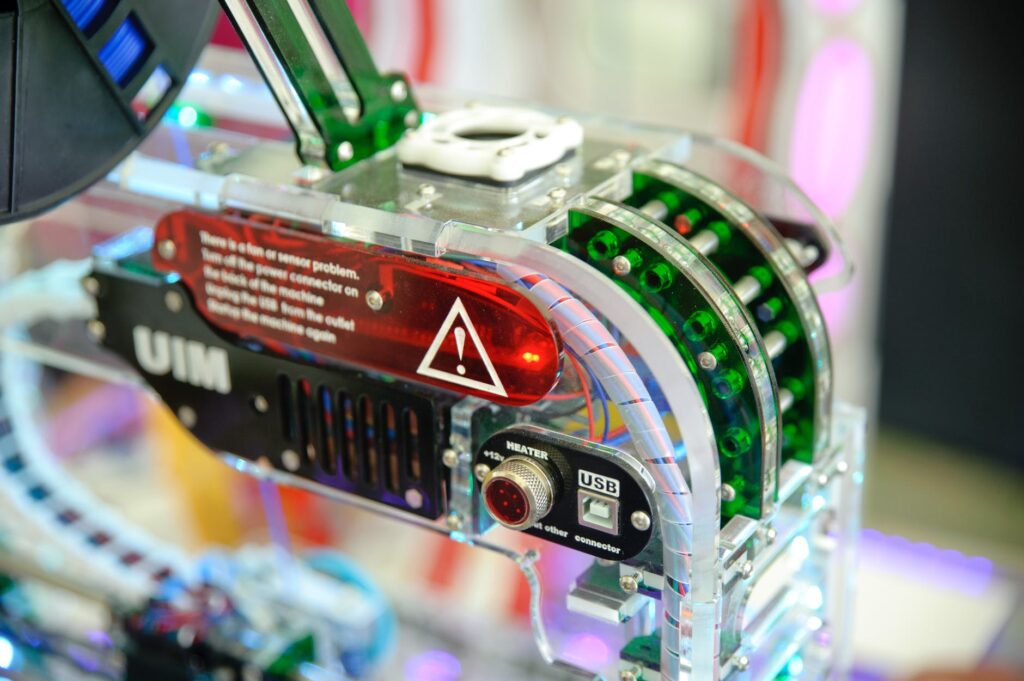
Was ist das Pareto-Prinzip? Haben Sie schon einmal von der 80/20-Regel gehört? Es ist ein Phänomen, dass 80 % der Folgen auf 20 % der Ursachen zurückzuführen sind. Dieses Prinzip lässt sich in vielen Bereichen anwenden, z. B. in der ökologischen Umwelt, in gesellschaftlichen Strukturen, im Zeitmanagement bei der Arbeit und sogar in der Sprache. […]
Pareto Principle
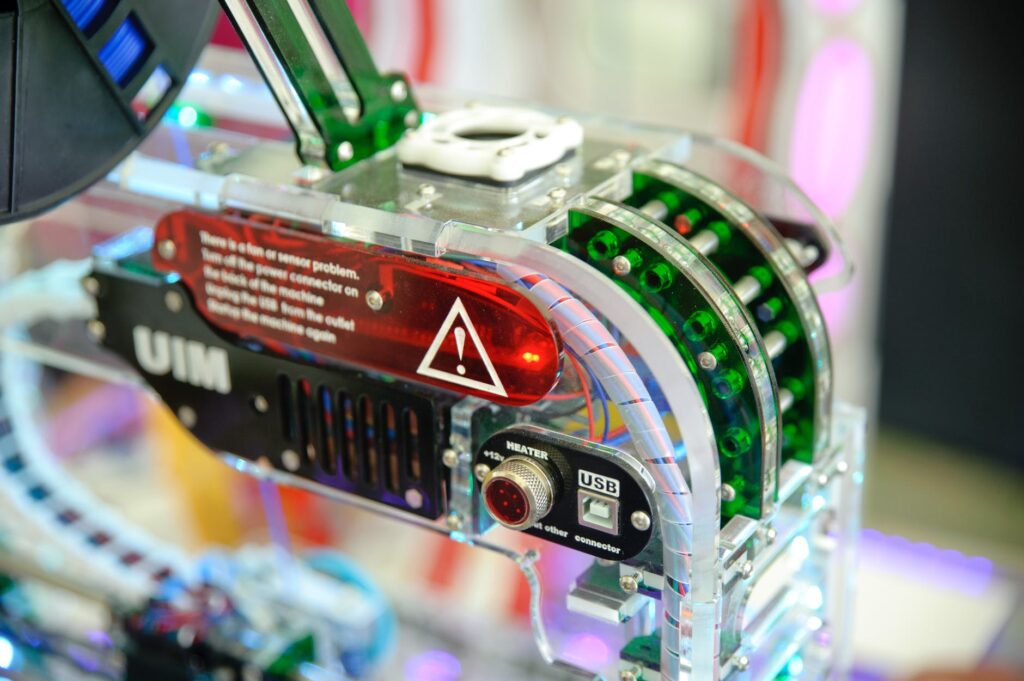
What Is the Pareto Principle? Have you ever heard of the 80/20 rule? It is the phenomenon that 80% of consequences come from 20% of causes. This principle can be seen in action across multiple areas of study like ecological environments, societal structures, work time management, and even language. To wrap our minds around it, […]
Pareto Principle
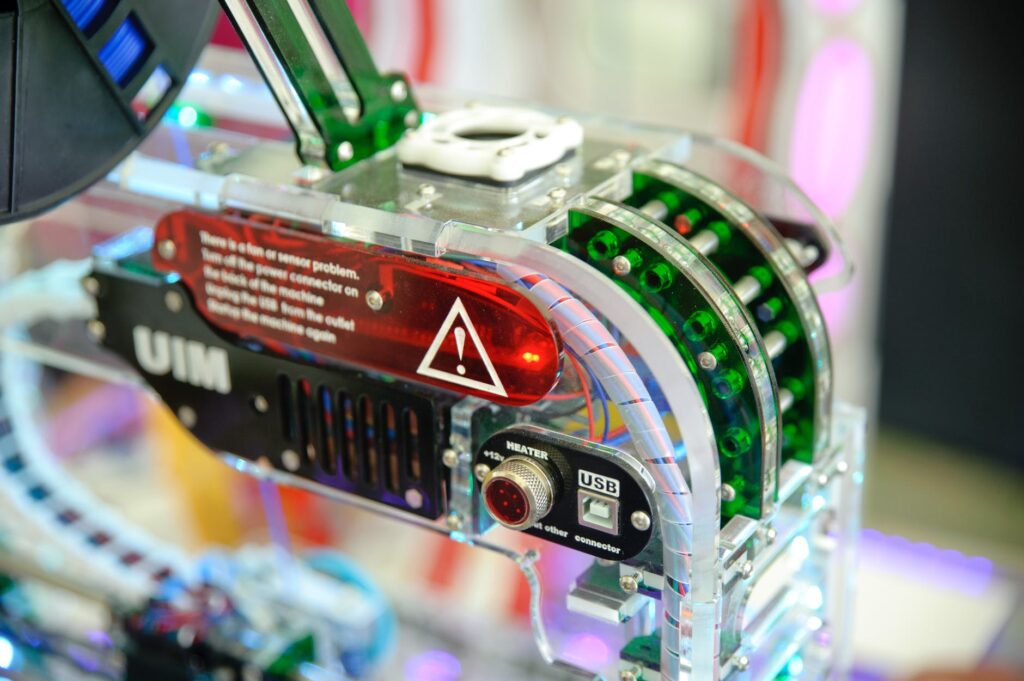
What Is the Pareto Principle? Have you ever heard of the 80/20 rule? It is the phenomenon that 80% of consequences come from 20% of causes. This principle can be seen in action across multiple areas of study like ecological environments, societal structures, work time management, and even language. To wrap our minds around it, […]
個人用保護具(PPE)
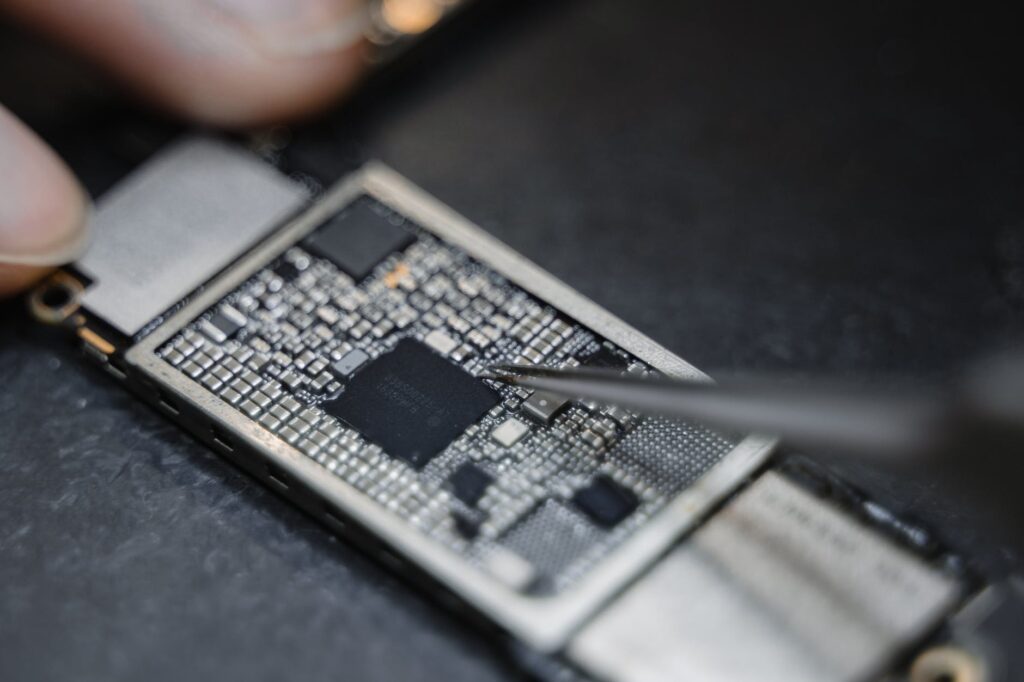
PPEとは? PPE(Personal Protective Equipment)とは、人を傷害から保護するための衣服や身につけられる器具のことを指します。 反射ベスト、ハードハット、安全メガネ、防護服など、挙げればきりがないほどです。 事故や災難は、私たちの日常生活の中で避けられない要素です。 日中は製造現場で働き、夜は養蜂をし、週末はペイントボールで遊ぶなど、PPEは数え切れないほどの人々を重傷や死から救ってきました。 個人用保護具は一見簡単そうに見えますが、PPEの手順を最適化し、従業員の安全を保証するための知的な方法があります。 キーポイント PPE(Personal Protective Equipment)とは、着用者を怪我や害から守るための衣服や着用可能な機器と定義されます。 これには、ハードハット、反射ベスト、聴覚保護具などが含まれます。 PPEに関して言えば、安全は保護と同じくらい機動性が重要です。 作業指示ソフトを使用して、作業者がすべての作業で適切なPPEを使用していることを確認します。 PPEのカテゴリーとその用途 個人用保護具は、保護する部位によって分類されることが多い。 ここでは、最も一般的なPPEの種類と、それらが保護する身体の部位のリストを紹介します。 頭部保護具:ハードハットはその代表例ですが、落下物から頭部を保護するヘッドギアは、危険の多い環境では欠かせません。 顔面保護具安全眼鏡から溶接・研削用マスクまで、顔面保護具は不要な物質や粒子から顔を保護します。 耳の保護見落とされがちですが、耳の健康を維持するためには、耳の保護が重要です。 耳は、伸縮性のあるフォームプラグやノイズキャンセリングヘッドホンで保護することができます。 反射材を使用した服装:目立ちやすい服装は、スピードの速い環境では非常に有効です。 反射パッチは、ベスト、パンツ、ヘッドギアなど、あらゆる衣服に付けることができます。 足と手を守る:足と手は、人体の中でも特に怪我をする頻度が高い部位です。 これらの部位への傷害の多くは致命的なものではありませんが、傷害から安全を守ることは、多くの業界にとって依然として高い優先事項です。 手足の指を保護するために、鋼鉄製のブーツと手袋を使用します。 皮膚を保護するもの:着用者の皮膚を保護する衣服に分類されます。 例えば、溶接工は火花などの高温物から身を守るため、難燃性の溶接ジャケットを着用しています。 病院や危険物取扱所の職員は、皮膚に接触した場合に有害な薬剤から身を守るための完全な防護服を着用します。 呼吸器有害な化学物質を扱うときや、パンデミック(世界的大流行)のとき、肺から有害な物質を取り除くのに役立つのが呼吸器です。 使い捨てのフェイスマスクやフィルター付きのガスマスクなど、簡単なものでよいのです。 安全とは、邪魔をされないこと 製造現場は忙しいものです! 移動する車両、フロアプランの変更、危険物など、作業者を危険にさらす要因はたくさんあります。 ワーカーは安全を確保しつつ、機動性や環境への配慮も必要です。 私たちがunencumberedと言うとき、私たちは文字通りそれを意味します。 作業者が、業界で提供されているすべてのPPEを着用していると想像してください。 彼らは、歩くことができれば、保護するための歩くフン玉になるのです。 これは、彼らの意識を効果的に抑制し、より多くの事故を引き起こす可能性があります。 個人用保護具の意味する安全とは、オペレーターを事故や災害から守ると同時に、動作や視力など本来の能力を発揮できるようにすることです。 もし、安全眼鏡が曇りや傷で視界を妨げているのであれば、そのPPEは本来の目的から外れていることになります。 目は無事でも、滑ったり、つまずいたり、転んだりする経験をしやすくなります。 同様に、聴覚保護によってオペレーターが周囲の状況に気づかない場合、動いている車両に気づかない可能性が高くなります。 この2つの例は、個人用保護具の使用方法について、業界が賢くなる必要があることを示すものです。 製造環境、作業、プロセス、手順はそれぞれ異なる。 すべてのPPE要件を解決する機器や衣服は存在しませんが、スマートな解決策はあります。 PPEには、作業者が適切な作業に適切な機器を使用できるようにするための、インテリジェントなプロセスが必要です。 PPEや安全対策は、実施される作業に合わせてダイナミックに行う必要があります。 個人用保護具を有効に活用する 製造業では、安全眼鏡と鉄指靴が、常に着用しなければならない最低限のPPEの基準となっています。 しかし、ハードハット、聴覚保護具、防毒マスク、難燃性の衣服などが必要な作業についてはどうでしょうか。 企業では、業務の大半を占める作業に応じて、特定のPPEを常時着用することを示す包括的なルールを定めていることが多い。 これは安全性の大部分を確保するのに十分な方法ですが、施設のPPEニーズの100%をカバーするものではありませんし、すべての仕事の特定のニーズに対応するものではありません。 例えば、あるオペレーターが、金属研削盤を使用する珍しい作業を行おうとしています。 […]
Persönliche Schutzausrüstung (PSA)
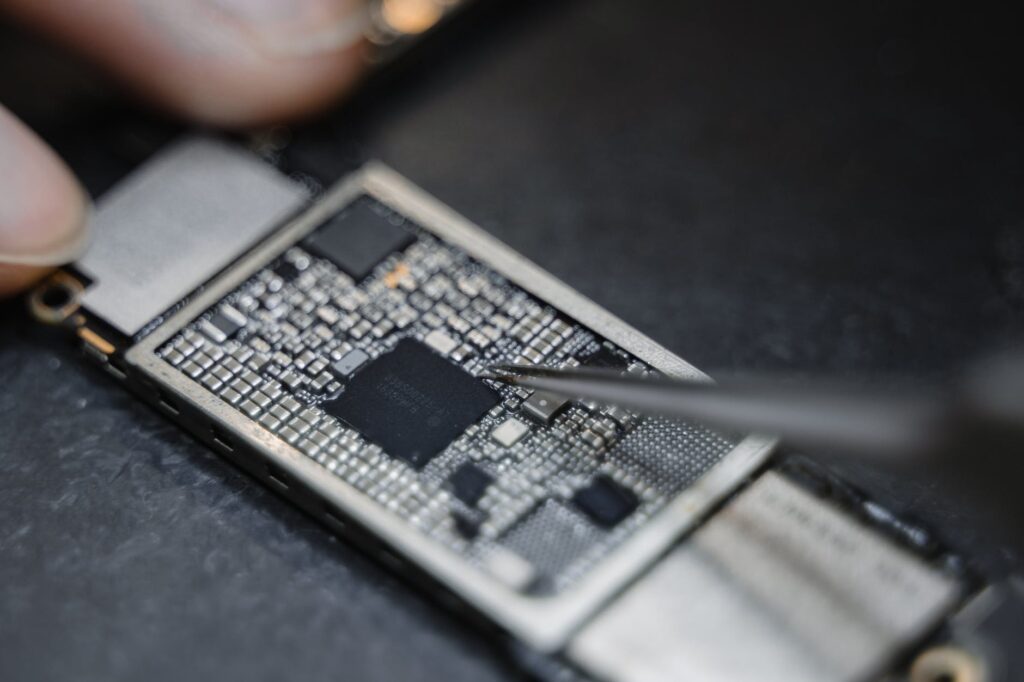
Was ist PSA? Als PSA (Persönliche Schutzausrüstung) gelten alle Kleidungsstücke oder tragbaren Ausrüstungsgegenstände, die eine Person vor Verletzungen schützen und/oder bewahren. Dazu gehören Warnwesten, Schutzhelme, Schutzbrillen, Gefahrgutanzüge und vieles mehr, was wir hier nicht aufzählen können. Unfälle und Missgeschicke sind unvermeidliche Faktoren in unserem täglichen Leben. Ob bei der Arbeit in der Produktion tagsüber, bei […]