Lead Time
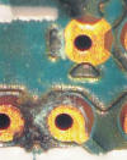
What is Lead Time Lead Time is the period between the customer placing an order and the product being delivered. It begins at the initiation of the purchase process and ends at the completion of the transaction. In many ways, Lead Time is the customer’s experience of the entire manufacturing process. Customers make their order, […]
リーン・マニュファクチャリング
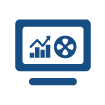
リーン・マニュファクチャリングとは? リーン生産方式とは、製造業が無駄を省き、顧客価値を最適化し、企業の生産性を高めるために用いる生産手法である。 付加価値を高める要素に焦点を当て、無駄を省く活動を行うことで、企業はより多くの価値を創造し、より高い業務効率を追求することができます。 本来、リーン・マニュファクチャリングはWin-Winのシナリオである。 核となる原則に注意深く従えば、リーン生産はコストを下げ、価値を高めることで、組織と市場の消費者にとって有益なものとなります。 キーポイント リーン生産とは、製品やサービスの価値を高めながら、無駄な活動を削減するプロセスです。 最も価値のある生産要素は、顧客に価値をもたらすものである。 リーン生産方式の基本原理は、トヨタ生産方式(TPS)にヒントを得ています。 リーン・マニュファクチャリングは、適切なバランスを見つけることです。 無駄をできる限り省くが、リーンを超えて生産に支障をきたさないようにする。 リーンの簡単な歴史 リーン生産方式は、1948年から1975年の間にトヨタ生産方式(TPS)によって初めて開発されました。 それ以来、リーンは、企業が模範とする非常に効率的な生産モデルとして、世界的に有名になりました。 トヨタ自動車の技術者である大野耐一と豊田英二は、主に自動車産業における無駄な在庫を軽減する方法としてこのシステムを作りましたが、今では多くの産業において、無駄を軽減し価値を高める他の方法と実践を包含するまでに成長しました。 リーンに影響を受けた生産手法の例として、カンバン、カイゼン、リーンシックスシグマ、DMAIC(定義、測定、分析、改善、管理)、DMADV(定義、測定、分析、設計、検証)などがあります。 それぞれ、製造環境におけるリーン手法のさらなる定義と強化に貢献します。 バリューとは何か? リーン・マニュファクチャリングを明確に理解するためには、顧客の視点から価値を理解する必要があります。 もし、ビジネスが顧客に価値を提供しないのであれば、ビジネスは成り立たない。 このように、リーン生産方式では、価値が最優先されるのです。 生産ライン内の価値は、3種類の活動に分かれる: 付加価値:消費者に価値を提供する活動である。 便利な機能、製品サポートなどを紹介します。事業付加価値:事業に対して直接的に価値を提供しつつ、顧客に対して間接的に価値を提供する活動です。 これには、保守、点検、データ保存などの活動が含まれます。非付加価値:消費者が目にしない、必要としない、そして/またはお金を払う気がない、不必要な活動です。 非付加価値活動は、リーン計画で最初に排除されるものの一部です。リーン生産方式では、常に消費者の視点を通して価値を考えます。 商品の価値を決めるのは、消費者です。 企業はその目標を達成するために、製品やオペレーションを適応させなければなりません。 消費者にとって直接的または間接的に付加価値をもたらさないものは、廃棄物とみなされ、除去されるべきです。 リーン生産方式の5つの原則 リーン・マニュファクチャリングは、以下の5つの原則を特徴としています。 価値を特定する:企業は、何が顧客に価値をもたらすかを特定する必要があります。 価値が明らかになれば、企業は顧客のニーズを満たす製品を設計する一方で、そうでない機能を削除することができるようになります。バリューストリームをマップする:バリューストリームとは、製品のライフサイクル全般を指します。 設計、材料、製造・組立、販売、お客様の使用、そして最終的な製品の廃棄までを含みます。 製品のバリューストリームをマッピングした後、メーカーはバリューストリームの中で付加価値のない要素やステップを削除することができます。フローを作る:制作にフローがなければ、時間を浪費していることになります。 アイテムは、バリューストリームを途切れることなく移動する必要があります。 リーン生産者は、効率的にオペレーションを整理して、流れ作業をしています。エスタブリッシュ・プル:この原則は、明確な需要がある場合にのみ、企業がその商品を生産することを要求するものです。 生産に流れを作るのと同じように、生産からお客様への移行も、どの時点でも滞らないようにしなければなりません。 市場に商品を送り込むのではなく、市場が生産ラインから商品を引き抜くため、大量かつ無駄な在庫を抱える必要がないのです。完璧を求める:リーン生産方式がビジネスに大きな影響を与えるには、企業文化が関与する必要があります。 すべての社員とシステムが、リーン・プラクティスを組織全体に広く適用し、完成させることを目指す必要があります。 廃棄物とは何か? 製造現場における「リーン」とは何かを正確に理解するためには、無駄とそれがどのように発生するかを明確に理解する必要があります。 トヨタ生産方式(TPS)によると、無駄は3つに分けて考えることができる。 ムダ(無用の長物):現在、廃棄物に関する議論の多くは、無駄な慣習を中心に行われています。 これらは、顧客に付加価値を与えないあらゆる活動である。 これは、ペーパーワークから非効率なロジスティックプランニングに至るまで、あらゆるものが含まれます。 製品やサービスの価値の流れの中で、無駄を生み出す活動や無駄な活動を排除・削減することである。ムリ(過重負担)です:ムリとは、操作の補助システムを外しすぎた結果です。 お客さまに直接付加価値を与えないシステムもありますが、それでもオペレーションには有用なものです。 真のリーン・マニュファクチャリングには、現代の製造業の課題に耐えうる柔軟性と弾力性が必要です。ムラ(凸凹):生産ラインは、バランスをとって流すことが必要です。 そうでなければ、必然的に非効率が発生します。 ムラは、顧客の需要(タクトタイム)や、製品ごと、作業者ごとの工程・サイクルタイムなど、生産のさまざまな領域で見られる。無駄を理解し、カットすることは、バランスをとることです。 リーン手法に取り組む企業は、無駄を省くべきですが、経営に支障をきたすほど深刻なものではありません。 リーンの8つの無駄 無駄をより深く、バランスよく理解するためには、「リーンの8つの無駄」を通して理解するのがよいでしょう。 これらは、DOWNTIMEという適切な頭文字を使って覚えることができます。 […]
Production allégée
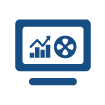
Qu’est-ce que la production allégée ? La production allégée est une méthodologie de production utilisée par les fabricants pour éliminer les déchets, optimiser la valeur pour le client et accroître la productivité de l’entreprise. En se concentrant sur les facteurs qui ajoutent de la valeur et en réduisant les activités qui sont source de gaspillage, […]
Schlanke Fertigung
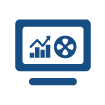
Was ist Lean Manufacturing? Lean Manufacturing ist eine Produktionsmethodik, die von Herstellern eingesetzt wird, um Verschwendung zu vermeiden, den Wert für den Kunden zu optimieren und die Produktivität des Unternehmens zu steigern. Durch die Konzentration auf wertschöpfende Faktoren und die Reduzierung von Aktivitäten, die Verschwendung verursachen, können Unternehmen mehr Wert schaffen und gleichzeitig eine höhere […]
Lean Manufacturing
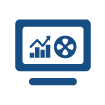
What is Lean Manufacturing? Lean Manufacturing is a production methodology used by manufacturers to eliminate waste, optimize value for the customer, and boost company productivity. By focusing on factors that add value and cutting activities that cause waste, companies can create more value while pursuing greater operational efficiency. Essentially, Lean Manufacturing is a win-win scenario. […]
Lean Six Sigma
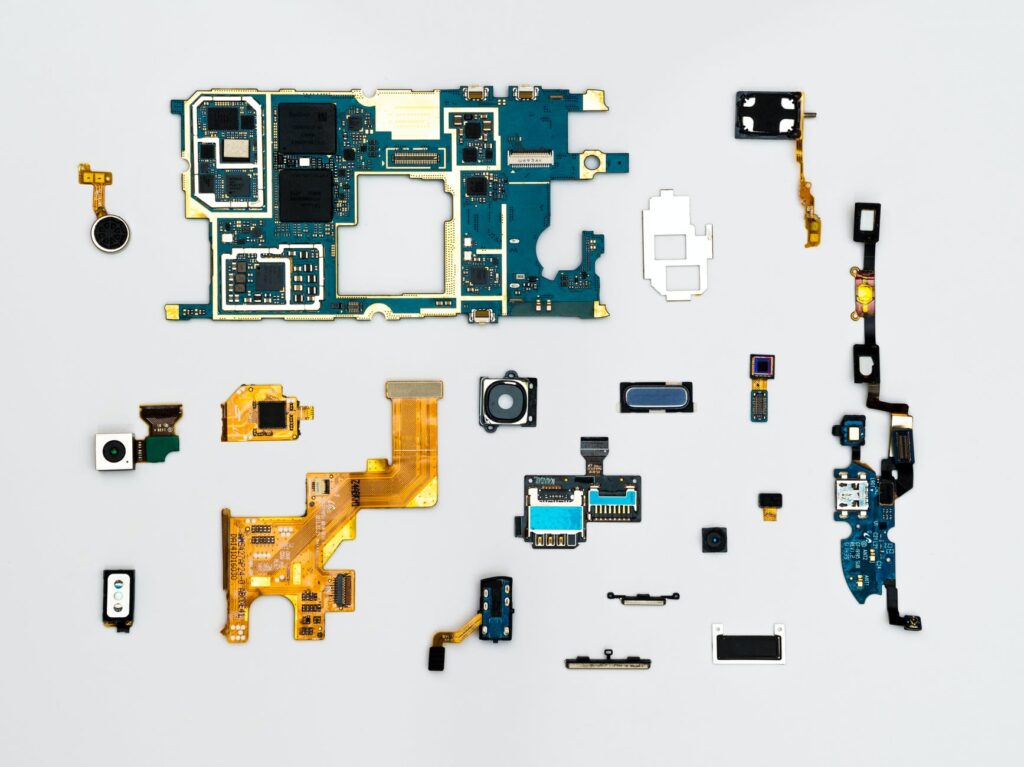
Au fil des années, les entreprises ont mélangé et assorti leurs philosophies de gestion, et nombre d’entre elles ont constaté que les méthodologies de production allégée et Six Sigma se complétaient bien. La méthode Lean Six Sigma a donc été progressivement adoptée dans le double but de réduire les variations et les déchets. PRINCIPAUX ENSEIGNEMENTS […]
Lean Six Sigma
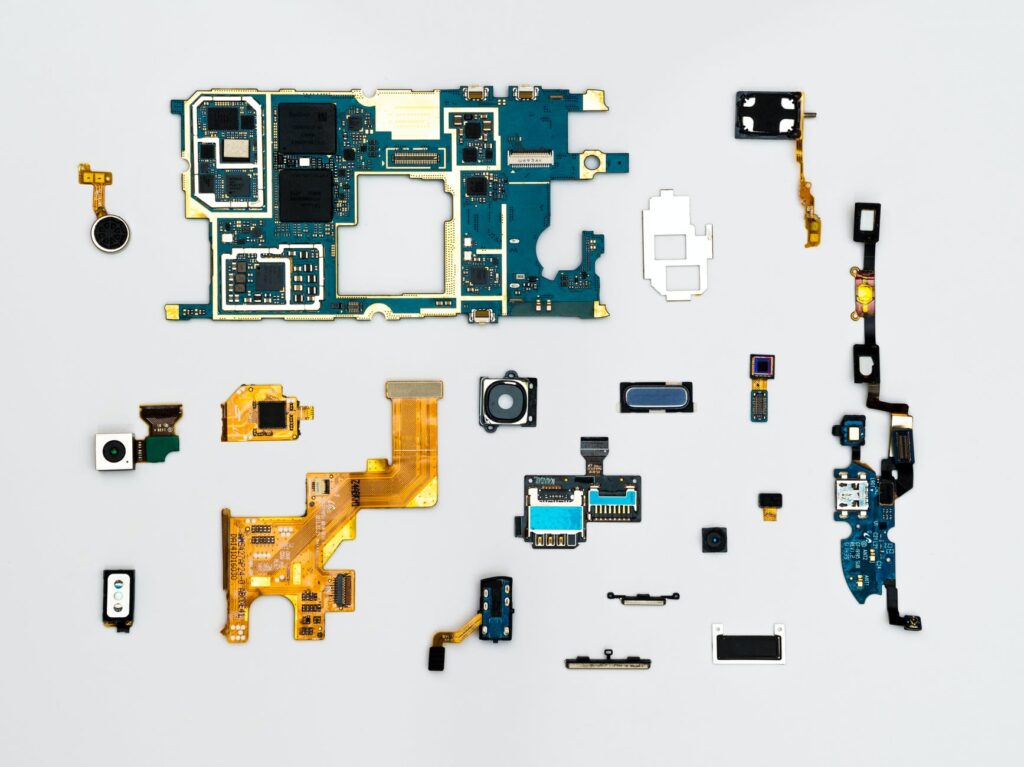
Da Unternehmen im Laufe der Jahre verschiedene Managementphilosophien miteinander kombiniert haben, haben viele festgestellt, dass sich die Methoden von Lean Manufacturing und Six Sigma gut ergänzen. So wurde Lean Six Sigma schrittweise mit dem doppelten Ziel eingeführt, sowohl Abweichungen als auch Verschwendung zu reduzieren. SCHLUSSFOLGERUNGEN LSS verbindet die datenbasierten Prozesse von 6S und die bedarfsorientierten […]
リーンシックスシグマ
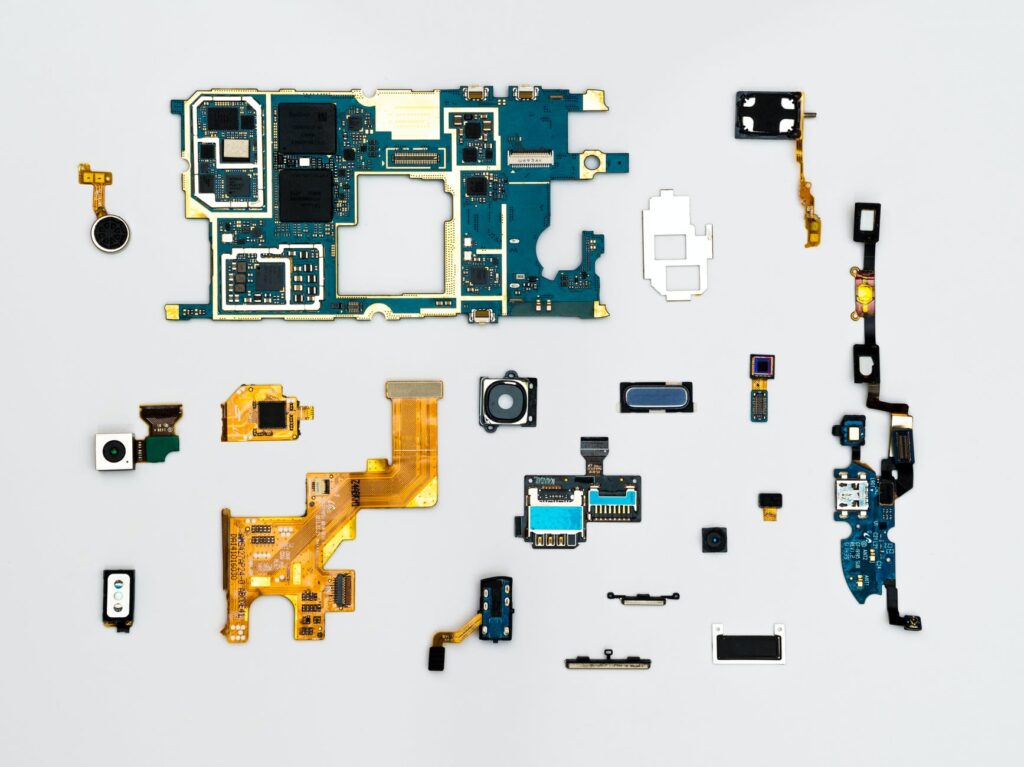
企業は長年にわたって経営哲学を混ぜ合わせてきたため、リーン生産方式とシックスシグマの方法論が互いに補完し合ってうまく機能していることを多くの企業が発見しています。 こうして、リーンシックスシグマは、バラツキとムダの両方を減らすという二重の目的を持って、徐々に採用されていきました。 キーポイント LSSは、6Sのデータベース・プロセスとリーンの需要ベース・プロセスを融合させたものです。 LSSで生産ラインを中心としたプロセスフローをリアルタイムに効率化 リーン・シックスシグマとは? リーン・マニュファクチャリングの基本 リーン生産方式とは、生産工程から可能な限り無駄を排除し、生産物の価値を最大限に維持することを基本とする手法です。 リーンの原理には、企業内のワークフローや社会組織を改善するためのさまざまなテクニックやツールが含まれます。 また、「ポカヨケ」のようなツールは、生産サイクルのボトルネックの特定に非常に有効です。 リーンの基本は、工業生産における最も一般的な8つの無駄を列挙したDOWNTIMEという頭文字に言及しています: Defect – エラーや失敗過剰生産 – 販売可能な量以上の製品を作ることWaiting – 機械や演出を待っている時間。活用されていない人材 – 活用されていない社員のスキル輸送 – 物流・ロジスティクス在庫-売れ残った製品は倉庫に置くとコストがかかるモーション – リソースの誤用と組立ライン内の動きExtra Processing – 価値を提供しない過剰なエンジニアリングこのような無駄を洗い出し、生産から排除することがリーン生産方式の最大の目標です。 ムダを発見する手段は、主に生産ラインを実際に歩いてみて、質的に何が起こっているのかを「自分の目で確かめる」ことです。 シックスシグマの基礎知識 シックスシグマは、統計分析に基づく問題解決プロセスの活用により、製品のばらつきや不良を減らすことに主眼を置いています。 シックスシグマで使われるツールには、DOE、パレート図、バリューストリームマップなどがあります。 シックスシグマプロセスの原則は、頭文字をとってDMAICを指します: お客様の視点からプロセスの境界と期待値を定義する。現在存在するプロセスの定量的な性能を測定する。相関するデータを分析し、根本的な問題を特定する。代替ステップを開発し、テストすることでプロセスを改善する定期的なメンテナンスにより、プロセスの継続的な成功をコントロールする。DMAICメソッドで定義された計画と実行のプロセスは、100万個の部品製造あたり、つまり100万個の「機会」あたりの不良件数を確実に少なくするように設計されています。 この低欠陥プロセスの開発手段は、主に問題点を定量的に視覚的に表示する高度な統計分析チャートにある。 リーンシックスシグマはシックスシグマとどう違うのか? その差はわずかですが、それでも重要な意味を持つほど明確です。 まず、リーンシックスシグマは組織全体の効率化に重きを置いているのに対し、シックスシグマは製造業のサプライチェーンに特化しています。 これらは必ずしもガイドラインではなく、あくまで一般論であり、長い時間をかけて証明されたものです。 しかし、2つの哲学の間で共有される技術やツールが増えれば、両者の区別はさらに薄れていくに違いない。 シックスシグマがエラーの特定を優先するのに対し、リーンシックスシグマはエラーの予防を優先する。 また、出力を測定する管理図では、データに現れてから問題を特定することが容易である。 後者のワークフローやカンバン表は、ばらつきを未然に防ぐのに役立っています。 この区別は実際に重要か? 怒らないでください、でも答えはイエス…そしてノーです。 もし、あなたが同僚とリーン原則について何気なく話していて、管理図やばらつきの低減について触れたとしたら、シックスシグマやリーン製造ではなく、リーンシックスシグマと言ったとしても、彼らは混乱しないでしょう(黒帯シグマのカードを持っている専門家は別です、その場合は講義を受ける準備をしましょう!)。 しかし、そうではなく、理論的には、この2つの方法論はほぼ機能的に同等といえるほど重なり合っています。 しかし、本当に問うべきは、実際には、どの業務改善をどのように狙っているのか、ということです。 改善目標とそのためのツールを明確に示すことができなければ、何をきっかけにアプローチしても失敗します。 そうですね、適切な導入とステップアップのためには、これらの別々のアプローチの違いを、実務で発生するように理解し、伝えることが絶対に必要です。 例えば、顧客成功率の向上ではなく、生産プロセスの無駄をなくすことを目標にDoE(実験計画法)を使用している場合、これが無駄の削減という特定の目標を持ったリーンDoEであることを強調し、改善が必要なビジネスの他の領域と関連するリーンシックスシグマ全体のゲームプランにどうフィットするかを説明します。
Lean Six Sigma
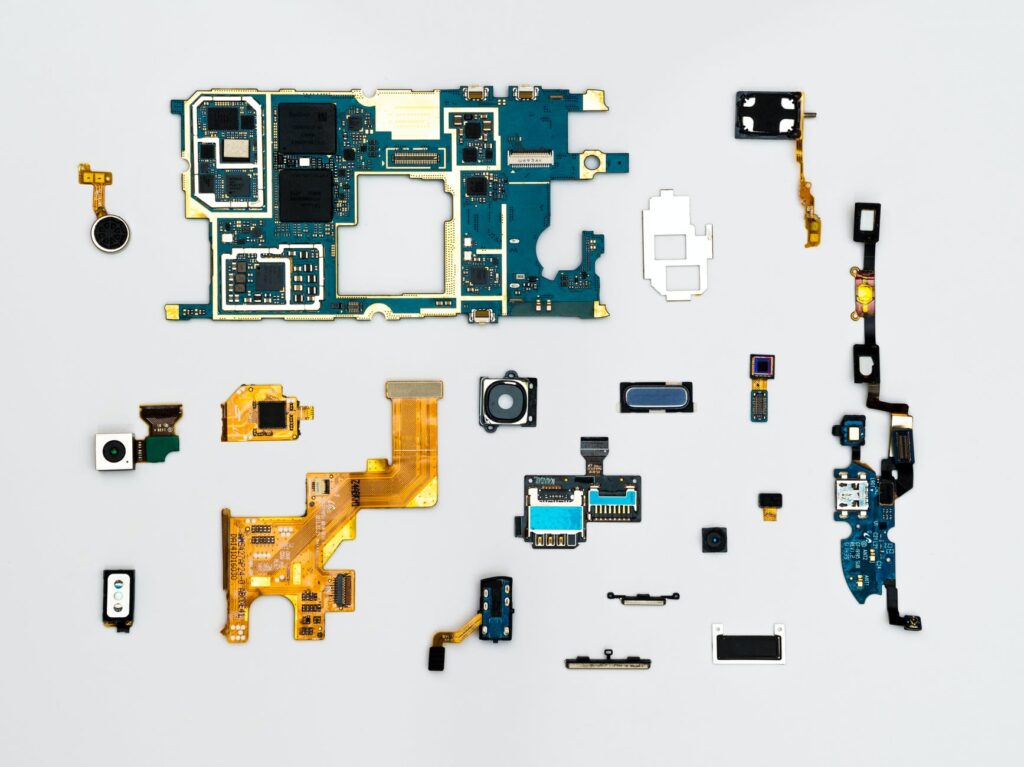
As companies have mixed and matched business management philosophies throughout the years, many have found that the methodologies of Lean Manufacturing and Six Sigma work well in complement with each other. Thus, Lean Six Sigma was gradually adopted through a dual minded purpose of reducing both variations and waste. KEY TAKEAWAYS LSS marries the data-based […]
オン・プレミス
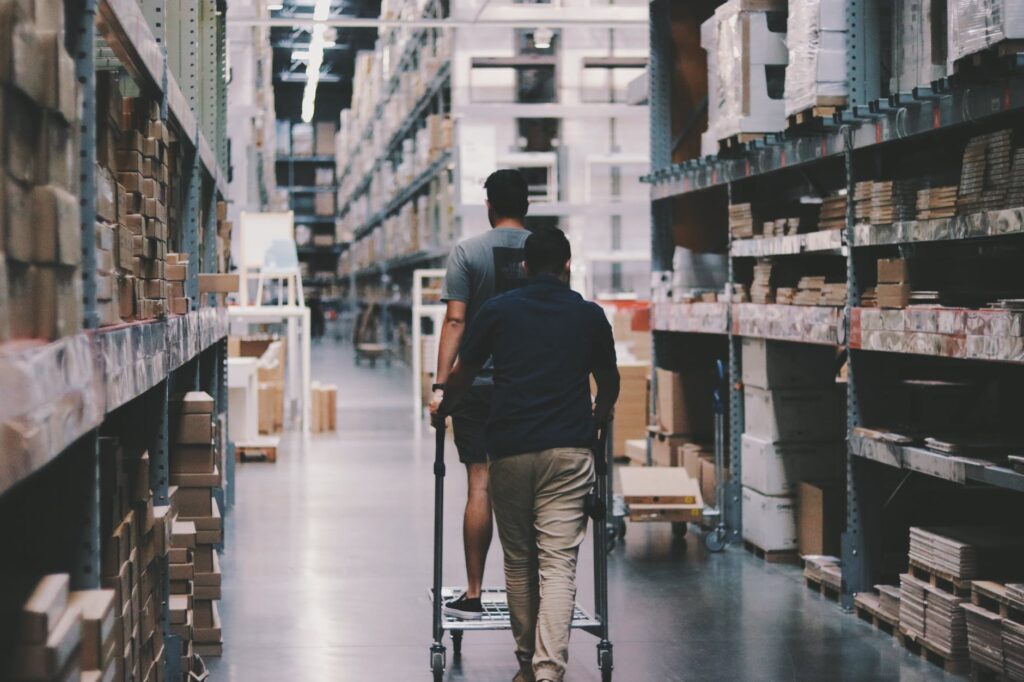
オンプレミスは、オンプレミスまたはオンプレムとも呼ばれ、お客様の所在地に物理的に設置されたプライベートサーバーで独立してホストされるライセンスソフトウェアの一種である。 クラウドコンピューティングを前提としたSoftware-as-a-Serviceの代替となるものです。 キーポイント オンプレース(または「オンプレム」)は、お客様の「敷地内」にインストールされるソフトウェアです クラウド型SaaSの対極にあるもの ITインフラは、オンプレミスソフトウェアモデルの延長線上にあります。 オンプレミスの例 オンプレミスツールには2種類あります: ソフトウェア オンプレムソフトウェアとは、お客様の敷地内にある物理的なサーバーにインストールされ、動作するアプリケーションのことをいいます。 SaaSのような従量課金制とは異なり、ライセンスは物理サーバーにダウンロードされるため、インターネットに接続されていなくてもアクセスすることができます。 オンプレミスソフトウェアの例として、Microsoft Office Suiteが挙げられます。 ハードウェア オンプレミスのハードウェアは、本当に機械のように物理的に存在する道具を表現するための空想的な方法です。 IT環境では、オンプレミスハードウェアの例として、サーバールームにあるハードディスクが挙げられます。 どのような組織や企業でも、通常、オンプレミスのITハードウェアが何らかの形で存在しています。 オンプレミスとクラウド(SaaS)ソフトウェアの比較 オンプレミスとクラウドベースのアプリケーション、どちらのタイプのソフトウェアにも欠点と利点があります。 さらに、ある会社にとって適切なパッケージと、別の会社のソフトウェアソリューションは全く異なるものに見えるかもしれません。 これらのオプションのメリットとデメリットについて読む際には、ご自身のビジネスのニーズを一番よく知っているのは自分自身であることを念頭に置いてください。 例えば、法律事務所では、業務の大半が文書や電子メールアプリケーションに依存する通信業務であり、リアルタイムで常に更新する必要がないため、基本的なMicrosoft Officeスイートのみで運用することが可能です。 (最後にMicrosoft Wordをアップデートした時のことを思い出せるだろうか?それともみんなまだ2010年版を使っているのだろうか?)。 例えば、原材料のサプライヤーが、供給とリアルタイムの課題に応じて流通コストを計算する必要がある場合を考えてみましょう。 オンプレミスソフトウェアのメリット 自社のデータに第三者がアクセスすることがないので、プライバシーの確保に適しているアプリケーションの利用を管理者が完全にコントロールできるサプライヤーからの干渉や予期せぬ自動アップデートなしに、アプリケーションをフルカスタマイズすることが可能 オンプレミスソフトウェアのネガティブな点 社内のメンテナンスと将来のアドオンやアップデートに責任を持つ。APIを自作(または外注)する必要がある当初、専門的な知識を持ったユーザーがいなかったために、ソフトウエアのアプリケーションの能力を十分に発揮できない可能性がある。 SaaSのメリット 従量制で、必要な分だけ容量や処理能力を確保することができる瞬時に拡張でき、他のシステムとの相互運用が可能(複雑なAPIを構築する必要がない)場所を選ばないため、社員は必要に応じてどこからでもデータやファイルにアクセスすることができます。 SaaSのネガ サブスクリプションモデルのシフトにより、短期的なコストが増加する可能性があるソフトウェア・プラットフォーム間で多くの変更がなされた場合、企業が買い物をする際に混乱を引き起こす可能性がある。クラウド経由でデータを保存するため、サイバーセキュリティに不安がある。また、オンプレミスとクラウドの両方を活用したり、あるアプリケーション(物理的な機械を制御するものなど)はオンプレミスで、他のアプリケーション(電子メールなど)はオフサイトで利用するというハイブリッドモデルを選択することも十分可能です。 例えば、VKSの作業指示ソフトは、SaaS型とオンプレミス型があり、クライアントがツールをカスタマイズすることができます。 オンプレミスソフトウェアの要件 ITと管理インフラは、オンプレミスの能力の延長であることを忘れないでください。 つまり、お客様のオンプレミスソフトウェアは、サプライヤーではなく、お客様の責任でメンテナンスする必要があるのです。 もし、他のシステムとの互換性がないなどのインフラ的な問題や、ITスタッフの不足などにより、十分に活用されていないのであれば、その効果は大きく減少することになります。 Microsoft Office 2010を購入し、長年使っていても、突然Microsoftを呼び出して最新バージョンにアップデートするよう要求することはできませんよね。 まず、最新バージョンはもともとダウンロードしたコードに書き込まれているわけではないので、不可能でしょう。 2つ目は、旧バージョンと全く同じ用途であっても、仕様が全く異なる別製品であることです。 これを解決する一つの方法は、コストのかかるハードウェアやソフトウェアの変更を取り入れる前に、IT部門の基盤を構築することです。 また、そのような場合、サプライヤーが提供する管理サポートが追加されるため、SaaSソリューションにこだわることもできます。 また、社内体制を整えた後に、そのソフトウェアでは対応しきれなくなった場合、他のプラットフォームを試すことができるのもメリットです。 しかし、スマートファクトリーの重要なツールセットであるIoTデバイスを理解する上で、オンプレミスとクラウドの違いを認識することは有益である。