Qu’est-ce que l’AGV ?
L’AGV ( Automated Guided Vehicle) est un type de robot mobile utilisé pour la manutention de matériaux dans diverses industries, y compris l’industrie électronique. Les AGV sont conçus pour suivre un chemin prédéterminé dans une installation, en utilisant diverses technologies telles que les lasers, les aimants ou les systèmes de vision pour naviguer et localiser leur position.
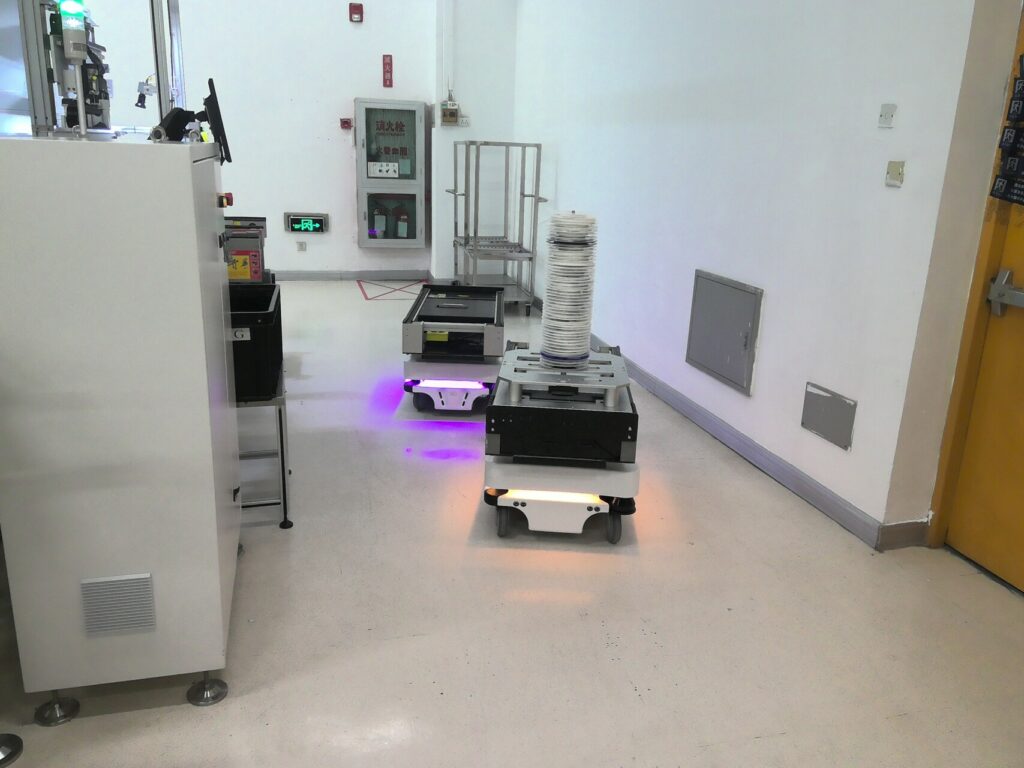
Dans l’industrie électronique, les AGV peuvent être utilisés pour transporter des matériaux et des composants entre différentes zones d’une installation, par exemple entre l’entrepôt et la ligne de production. Ils peuvent également être utilisés pour déplacer des produits finis vers des zones de stockage ou d’expédition. En automatisant ces tâches de manutention, les AGV peuvent contribuer à améliorer l’efficacité et à réduire le besoin de travail manuel.
Les AGV peuvent également être programmés pour effectuer d’autres tâches, telles que le tri et l’organisation des matériaux, et peuvent être intégrés à d’autres systèmes et équipements d’automatisation pour créer une ligne de production entièrement automatisée. Dans l’ensemble, les AGV peuvent contribuer à améliorer la productivité et à réduire le risque d’erreurs dans les processus de manutention dans l’industrie électronique.
Types d’AGV
Il existe plusieurs types d’AGV, notamment
- AGV guidés par des rails : Ces AGV utilisent des rails ou des fils encastrés dans le sol pour guider leur mouvement.
- Les AGV à guidage laser : Ces AGV utilisent des lasers ou d’autres capteurs pour naviguer et suivre un chemin prédéterminé.
- Les AGV guidés par la vision : Ces AGV utilisent des caméras ou d’autres capteurs de vision pour identifier leur emplacement et naviguer jusqu’à leur destination.
- Les AGV hybrides : Ces AGV utilisent une combinaison de différentes technologies, telles que des chenilles, des lasers ou des capteurs de vision, pour naviguer et suivre leur trajectoire prédéterminée.
Comment intégrer l’AGV au processus de stockage intelligent
Plusieurs mesures peuvent être prises pour intégrer les AGV dans un processus de stockage :
- Déterminer les besoins du processus de stockage : Avant d’intégrer des AGV dans un processus de stockage, il est important de comprendre les exigences et les besoins spécifiques du processus. Il peut s’agir des types de matériaux stockés, de la taille et du poids des matériaux, de l’agencement de l’installation de stockage et de la fréquence de manipulation des matériaux.
- Sélectionner le système AGV approprié : Une fois les besoins du processus de stockage identifiés, l’étape suivante consiste à sélectionner le système AGV approprié. Cela peut impliquer la prise en compte de facteurs tels que le type d’AGV (guidage par chenilles, guidage par laser, etc.), la capacité de l’AGV, la largeur et la hauteur de l’AGV, et la source d’énergie (électrique, diesel, etc.).
- Concevoir le système AGV : Le système AGV doit être conçu pour répondre aux besoins spécifiques du processus de stockage. Il peut s’agir de déterminer les itinéraires que les AGV suivront, les lieux où les matériaux seront stockés et ceux où ils seront chargés ou déchargés.
- Mettre en œuvre le système AGV : Une fois le système AGV conçu, il peut être mis en œuvre dans l’installation de stockage. Il peut s’agir d’installer l’infrastructure nécessaire (rails, lasers, capteurs, etc.), de programmer les AGV et de former le personnel à l’utilisation du système.
- Tester et ajuster le système AGV : Une fois le système AGV mis en place, il est important de le tester et de l’ajuster pour s’assurer qu’il fonctionne de manière efficace et efficiente. Il peut s’agir d’ajuster les itinéraires suivis par les AGV, d’ajuster la vitesse à laquelle les AGV fonctionnent et d’apporter toutes les modifications nécessaires au système.
Globalement, l’intégration des AGV dans un processus de stockage implique de planifier et de concevoir soigneusement le système AGV pour répondre aux besoins spécifiques du processus de stockage, puis de mettre en œuvre et de tester le système pour s’assurer qu’il fonctionne de manière efficace et efficiente.
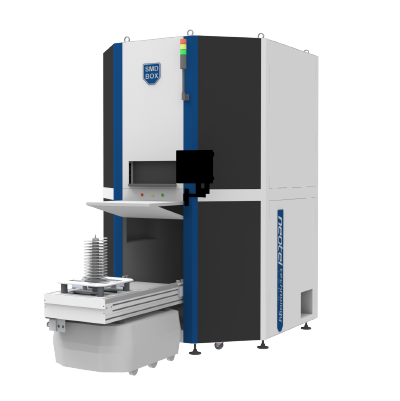
Cinq avantages de l’utilisation de l’AGV pour la manutention de matériaux
Les opérations de manutention peuvent bénéficier de l’utilisation d’AGV pour plusieurs raisons :
- Amélioration de l’efficacité : Les AGV peuvent transporter des matériaux rapidement et avec précision, sans intervention humaine. Cela peut contribuer à améliorer l’efficacité globale du processus de manutention.
- Réduction du risque d’erreurs ou d’accidents : Les AGV peuvent réduire le risque d’erreurs ou d’accidents causés par la manipulation humaine des matériaux, car ils suivent des chemins prédéterminés et ne nécessitent pas d’intervention manuelle.
- Augmentation de la capacité : Les AGV peuvent manipuler des charges plus importantes que les humains, ce qui permet d’augmenter la capacité d’une opération de manutention.
- Amélioration de la sécurité : Les AGV peuvent contribuer à améliorer la sécurité sur le lieu de travail en réduisant le risque d’accidents ou de blessures causés par la manipulation humaine des matériaux.
- Flexibilité accrue : Les AGV peuvent être facilement programmés pour suivre différentes trajectoires ou effectuer différentes tâches, ce qui les rend très flexibles et adaptables à l’évolution des besoins en matière de manutention.